EUROBAT discusses the importance of continued battery innovation and outlines potential areas to be addressed by battery research and development.
Eurobat is the association of Automotive and Industrial Battery Manufacturers and their subcontractors in Europe, the Middle East, and Africa. Representing the European battery industry, EUROBAT covers all mainstream battery chemistries available on the market: lithium, lead, nickel, and sodium.
Battery innovation is an ongoing process, in the 19th century it was basically driven by continuous efforts to develop a robust longer-lasting source of electricity that could provide reliable energy and power output. This effort resulted in lead-based battery products, a technology that has been a cornerstone for centuries and is still successfully used in today’s applications.
In the 20th century, battery innovation was driven by the emerging applications of the time, such as portable electronics, telecommunication, automotive vehicles, railway rolling stock, aviation, ships and submarines, satellites and the need for Uninterruptible Power Supplies (UPS). Each application demanded more specific battery characteristics, resulting in significant diversification of battery products. The development of lithium-ion batteries in the late 20th century complimented the widely used, affordable and proven safe lead-based technologies, thanks to their higher energy density and relatively low weight.
Today’s drivers for battery innovation are broader and more complex. Not only are batteries optimised with specific characteristics for specific applications, they are developed to meet Europe’s objectives regarding the environment, energy independency, security of raw materials supply, and further electrification of transportation and other sectors. In this new context, EUROBAT initiated a White Paper Batteries Innovation Roadmap 2030 in June 2020. This was updated in June 2022 in order to re-assess the market and technology evolutions for all four mainstream and future promising technologies, in relation to the applications they serve.
The roadmap highlights the state-of-the-art and innovation potential of each of the various mainstream chemistries:
Lead-based battery R&D
Lead-based battery development continues to be important, especially with the implementation of new innovative materials (like synthetic expanders, nano-based carbon materials, new alloy compositions) and improved battery design.
Their potential lies in application-specific innovation, such as improving dynamic charge-acceptance for automotives at uncompromised high temperature durability. Similarly, for specific industrial applications in the field of stationary and off-road transportation, they could be important in improving the energy and power densities with improved cycle-life.
Thin Plate Pure Lead (TPPL), Bipolar and Carbon Enhanced Lead Acid batteries are promising candidates for increased service life, PSOC operation, and improved power density. The outstanding feature in this process is that these improvements have been tailored to the particular applications.
In addition to fundamental research that enhances the electrolytes, materials, and components used, the introduction of smart battery operation modes also holds potential, positioning this battery chemistry in a leading role for specific automotive and industrial applications by 2030.
Lithium-based battery R&D
Currently, the most promising technology, the major requirement for higher energy densities to achieve increased driving range is directly linked to e-mobility. This results in a development roadmap for 2030 that mainly considers the lithium-based technologies based on modified Nickel Cobalt Manganese Oxide (NMC) materials, with increased nickel and reduced cobalt content in combination with high capacitive anode materials with carbon/silicon composites. Solid state technology is also targeted to increase the energy density and improve the safety aspect.
Due to the variety of possible combinations of cathode and anode materials, the resulting Li-ion batteries show specific and individual performance characteristics suitable for different kinds of applications.
The development of Li-ion technologies suitable for industrial and automotive applications is still a challenge in terms of alternative material research, activating extraction processes, ethically sound mining, recycling and safety.
In addition to NMC based lithium-ion technology, LFP (Lithium Iron Phosphate) is the favoured choice for stationary applications, particularly due to long cycle life. Ongoing R&D is steering towards ‘intrinsically safe’ Lithium Manganese Iron Phosphate (LMFP) with higher energy density. Both LFP and LMFP are devoid of critical raw materials like nickel and cobalt.
Nickel-based battery R&D
Thanks to decades of safe use under the most extreme climates, cycling and/or fast charging operating conditions, nickel-based batteries (nickel cadmium and nickel metallhydrid (NiMH)) are still used in special and niche applications, with different designs.
The technology can be further developed both for existing applications and as a replacement solution, due to its key performance properties in extreme conditions. Nickel-based batteries are among the electrochemical storage systems that should be considered to remain in the market for targeted industrial applications over the next decade.
Sodium-based battery R&D
In contrast to other battery types, high-temperature nickel based batteries (operation temperature >300°C) consist of liquid-electrodes and a solid electrolyte. Commercially available representatives are sodium nickel chloride (NaNiCl), and the sodium-sulphur battery (NaS), which are used in stationary larger back-up power and load-levelling applications.
Both technologies still have room to improve in regard to energy efficiency (thermal losses due to heating necessary to maintain the cell temperature), internal resistance (which is positive for NaNiCl). Other factors to research and consider are the high demand for nickel and the complex modular construction.
Nowadays, the primary focus of sodium-based battery R&D is the promising drop-in technology of room temperature Sodium-Ion battery (SIB). The working principle is comparable to Li-Ion batteries, with the major advantages in comparison being the use of non-critical materials and potential of lower costs.
EUROBAT Innovation Roadmap 2.0
The current EUROBAT Innovation Roadmap 2.0 also takes into account the innovation potential of most promising technologies including: lead bipolar, sodium-ion room temperature, post-lithium-ion all solid state Gen. 4b and Gen. 4c, and Lithium Sulphur and Lithium-Air Gen 5. Regarding each, it is necessary to consider why it is important to continue their developments.
Taking into consideration the projected timelines for both upscaling European production capabilities, and for innovations to enter the markets, combined with promising recent market predictions (demand side), we can conclude that li-ion and lead-based batteries will remain the dominant battery technologies in 2030.
The Avicenne report September 2023 commissioned by EUROBAT predicts a global battery market of 4150 GWh, of which 3360 GWh lithium-based and 774 GWh lead-based technologies.
The EUROBAT Batteries Innovation Roadmap is a living document.
We anticipate a third edition to be released during the EUROBAT Annual Event in Brussels on 4-5 June, 2024. In this document we will be able to evaluate the impact of the different EU policy initiatives and new legislation in place since we published the roadmap 2.0.
EUROBAT supports the European Commission’s European Battery Alliance (EBA) and aims to remain at the forefront of technology developments across various sectors. This includes scaling up competitive and sustainable domestic production capacities for all technologies, from raw materials to battery pack production.
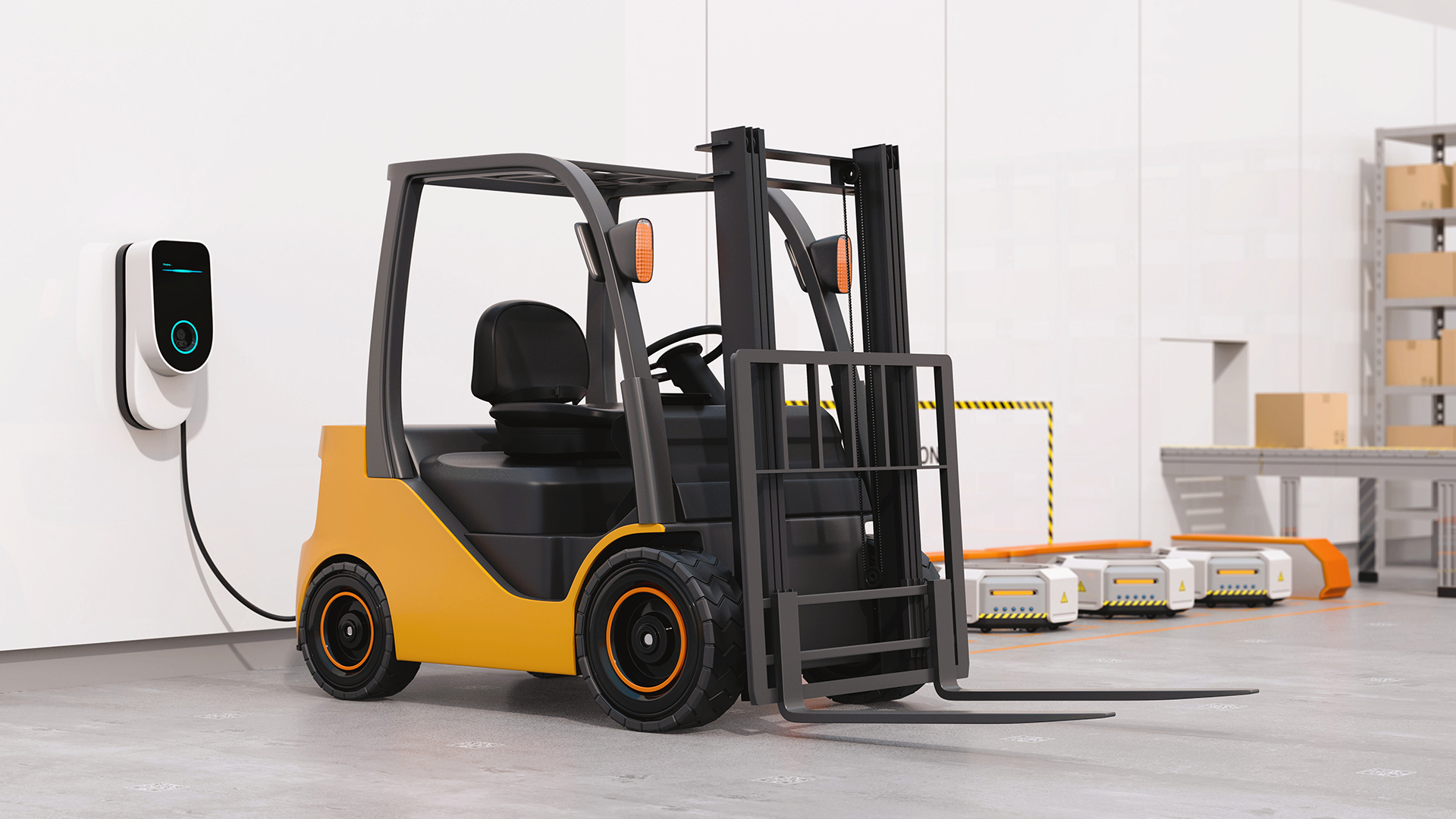
Major challenges to address
In today’s situation, we can already confirm that our technology leadership, which we will describe in the next update, will involve new areas of innovation, such as manufacturing processes and recycling, with a strong focus on developing a circular economy and incorporating sustainability aspects, whether or not with governmental and/or private-led R&D funds.
Other transversal aspects and major challenges that need to be addressed with R&D are data management, digitalisation and standardisation needs (implementation of the battery mandate M/579 and improve the use of the Battery Passport in future) in order to better direct waste streams, to meet higher collection rates (all elements) and to maximise the use of recycled primary and secondary materials in new batteries (all technologies).
The recently introduced Net-Zero Industry Act, as part of the Green Deal Industrial Plan, and the reform of the Electricity Market Design will further attract R&D on battery integration in many applications, as well as investments to scale up manufacturing of clean technologies (including battery manufacturing). In short, the future of the European battery manufacturing industry presents challenges that we must overcome to succeed.
Please note, this article will also appear in the sixteenth edition of our quarterly publication.