Professor Paul Anderson, Principal Investigator for the ReLiB project, and Dr Gavin Harper, Faraday Institution Research Fellow, explain what the project will achieve concerning the sustainable management and recycling of lithium-ion batteries.
Despite the COVID-19 pandemic, 2020 saw electric vehicle (EV) market growth across Europe, with plug-in vehicles making up 10.5%, compared to only 3% in 2019. This rise equates to more than a million EVs registered, effectively doubling the amount to more than two million now on our roads. This rise, which will continue, means the current methods of recycling lithium-ion batteries (LIBs) are likely to be insufficient in the future. A solution must be found, to minimise the environmental footprint of EV LIB decommissioning, ensure access to critical raw materials and thus minimise the environmental impact of primary extraction.
The Birmingham Centre for Strategic Elements & Critical Materials (BCSECM) Faraday Institution Recycling of Lithium-Ion Batteries (ReLiB) project has been addressing the technological, economic and legal infrastructure required to optimise the efficiency of material management from lithium-ion batteries originating from the automotive sector. It aims to ensure ‘the sustainable management of lithium-ion batteries when they reach the end of their useful life in electric vehicles.’
Lisa Carnwell, Managing Editor of The Innovation Platform, spoke to Professor Paul Anderson, Professor of Strategic Elements and Materials Sustainability, and Principal Investigator for the ReLiB project, and Dr Gavin Harper, Faraday Institution Research Fellow, about the hopes for the efficient, safe, and sustainable management of recycling lithium-ion batteries.
What does the current landscape look like regarding the recycling of lithium-ion batteries?
Dr Gavin Harper (GH): The current recycling processes mainly involve large amounts of manual intervention, and with the volumes that we anticipate, that will be quite an inefficient way of doing things. We want to look towards a more efficient, automated system that leverages robotics and AI in the pursuit of being able to recycle batteries quickly and efficiently.
The recovery rates of some existing recycling processes are something to bear in mind. We carried out a comprehensive review of this in our open access paper that appeared in the Nature journal: Recycling Lithium-ion Batteries From Electric Vehicles.
After comparing different lithium-ion battery recycling processes, we found that some of the current methods result in the loss of many materials. We want to move towards more efficient processes that are less energy and resource-intensive, result in higher rates of material recovery and higher rates of value recovery. In addition, it is not just the technical challenge of recycling, but there are other important factors to consider around the economics, legal, and regulatory landscape.
Professor Paul Anderson (PA): A critical point about using pyrometallurgy to extract and purify materials is that much of the material, including the carbon from the anode, the polymers, and the electrolyte, is burned, which creates CO2. Although you do recover energy, the materials are not recovered, so it is not circular. The lithium also ends up in a slag phase, where it is difficult to achieve anything usefully or economically.
The current recycling approach effectively puts the battery into a giant industrial shredder and chops it into tiny pieces (creating what we call ‘black mass’). However, we should be aiming to separate the components mechanically, manually, or by automation. By doing this, we would preserve the value streams of materials and remove further processing downstream. This would enable us to recycle not only valuable materials like cobalt and nickel but also cheaper cathode materials like lithium-iron-phosphate, which have less value. Those are the two research challenges we are addressing in ReLiB: cost-effectively achieving the dismantling process and preserving the value of materials streams.
The simplest way for the industry to passivate batteries (due to their high voltage, fire hazard and toxicity) is to put them under inert gas, water, or cooled down supercritical carbon dioxide. Once sent through the shredder, this transforms the battery (which has several hazards) into just one hazardous material, black mass. The logic of this process, however, is not sound. We should aim to keep materials that are well separated in the device at its end of life apart and preserve the materials in the highest value state, leading to improved efficiencies.
The European Union are placing immense importance on recycling and securing access to raw materials. What efforts are being made to recycle and ensure access to materials, and what are our challenges?
GH: We currently have a two-sided problem. On the one hand, we have a waste management challenge, and on the other, we have a massive opportunity in terms of raw materials. The UK has the ambition to manufacture batteries, but we do not necessarily have access to all the raw materials that we need. That will be challenging because we are competing against other countries that have proactively invested in the various supply chains and secured access to those different materials.
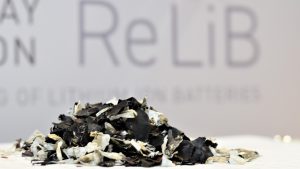
The UK is trying to secure future access to raw materials because, in the early stages of the industry, we need access to the primary materials as there are not enough scrap batteries in the system. The other thing to bear in mind is that in the early stage of the lithium-ion battery recycling industry, many of the batteries that need to be recycled will not be end of life from electric vehicles. Instead, they will be production scrap from manufacturing operations.
Another of our papers, which appeared in Science, looks at the global impact of the EU Battery Regulation,1 which may have some unintended consequences. In the paper, we mention that ‘if left unaddressed, the Regulation, at worst, could hamper climate change mitigation targets and fall short of its intentions to promote a circular economy and establish a socially acceptable raw material supply chain.’
From a recycling point of view, one of the biggest challenges is that we need to look at how we design batteries and optimise them for the whole life cycle. It is essential, to begin with the design of batteries and how we make the battery cell, so it is much easier to take apart and analyse the raw materials at the end of their life.
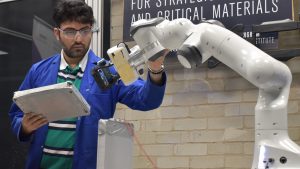
Companies worldwide are engaged in the challenge of the scale-up of production, which will require raw materials. In the market’s later stage, recycled batteries will provide a great source of raw materials.
PA: Besides the recent announcements for two gigafactories in the North East, and intense lobbying for another to support car manufacturers in the West Midlands, the Faraday Institution estimates we will need a total of at least eight by 2040.2 Gigafactories are expensive to set up, and we will also need to secure raw materials supply. And, although the number of batteries currently available for recycling is relatively low, within five to 10 years, it could be a significant contributor to the raw material supply chain.
We recently produced a paper discussing the importance of design in lithium-ion battery recycling3 where we argue that product design should be an essential step in the recycling process. One of the fundamental challenges with current recycling is that almost nothing in the batteries, apart from cobalt and nickel, is economical to recycle.
Recycling is happening, primarily in Asia. Even in Europe, where recycling is taking place, materials are often shipped to Asia to recover the precious metals. This results in losing that value and control of those critical materials in the supply chain.
There are two main reasons why LIB recycling is costly. EV battery packs are large, so a great deal of dismantling work is required with special equipment and trained engineers or technicians before you ever get near any of the materials. Our efforts to automate that process will improve not only the economic side but also address safety concerns.
Gavin and I, along with others, have examined this issue of raw material supply, resulting in the publication of a sizeable report,4 which is mentioned in a recent House of Lords Select Committee report,5 and we understand that government departments are studying this seriously.
Every sector and region in the world wants to electrify. In the end, what might determine how quickly people can do it, is what different jurisdictions have to the suitable raw materials. We should not underestimate the influence this has on when and where gigafactories are planned and built. All companies involved need to ensure a very secure supply chain before contemplating the significant investment required.
In the House of Lords Select Committee report, I quoted data that by 2040, we might be able to source somewhere between 25% and 35% of our lithium and cobalt from secondary sources. Still, the main challenge facing the UK is that it does not recycle any lithium-ion batteries. Instead, many are sent abroad, for example to a facility in Belgium. Unless the UK develops its own facilities, recycled materials would be another import. Another cross-border issue is that recycling may have to be undertaken according to the EU Battery Recycling Directive standards.
GH: We have to deal with the batteries that are out there at the moment. And it depends on the manufacturer’s attitudes as well. Some Chinese firms have tweaked this concept of designing the battery to dismantle it easily in a way that some other manufacturers have not. Perhaps this foresight comes from the high degree of vertical integration in the Chinese battery industry — they realise that they will also have to recover materials from the battery at the end of life. Ultimately, this will be driven by industry. Still, we must keep pushing the case that these are valuable materials, and end of life considerations need to be high on the agenda.
PA: An important point to make is that none of the vehicles on the road are zero-emissions; the grid, the electricity, and the manufacturing are not zero-emissions. EU legislation is forcing manufacturers to see the writing on the wall, but far too little attention has been given to how green the end of life processes or de-commissioning will be. It would be a mistake to risk undermining the credentials of the EV revolution by ignoring this. It may be that our speedy push toward the introduction of EVs is not the greenest pathway and a more measured transition with better end of life and manufacturing processes, it might be a lower-carbon path.
Although we do talk a lot about design for recycling, this effectively is trying to solve next the decade’s problem and not the currently un-optimised batteries that are being produced now.
We also must look at the scale of the recycling issue. We are recycling now, but something that may work for the trickle of batteries we see now may not be acceptable when there are many more. Once you imagine the amount of chemicals, energy, and recycling plants required to manage a flood of batteries, the numbers soon stack up. To give you an idea of the scale of the global vehicle fleet, if we electrify just 2%, that is enough to stretch around the Earth. That is how many vehicles are in the world: it is a colossal number.
Another challenge is that of battery safety. How do we approach risk management for end of life lithium-ion batteries?
PA: Part of the future automation process is about making it safer for workers and operatives. But we must also think about an unscheduled end of life, including batteries involved in site accidents and vehicle crashes, for instance. If an electric car is involved in a severe accident, is the battery stable or not? How should you go about removing that from the site and safely recycling or disposing of it?
First responders must be trained in how to deal with an accident involving an electric vehicle. They will need to recognise hazard signs, when to move in, and when to give it a wide berth. A high proportion of people killed in road traffic accidents currently are because of fires caused by the engine in the petrol tank. EVs are inherently different regarding the chemicals and mechanics, but of course still contain a large high voltage battery full of energy.
A great deal of education needs to be done in EV accidents as they can be dangerous. However, I am not convinced they are necessarily more hazardous than conventional petrol or diesel vehicles. EV batteries are very safe and well-engineered devices, which is one of the reasons we find them so difficult to take apart. I believe that will change in time, and engineers will make them lighter and perhaps less robust.
We have to consider some of the issues of safety over the life cycle of batteries, including the end of life disposal, their potential reuse in a second-life application, recycling and unscheduled end of life as described above.6
If reusing materials in batteries is key to achieving circular economy ambitions, what materials are currently being removed during the recycling process, and what improvements are the industry hoping to make moving forward?
PA: The only metals reused commercially are (semi-) precious metals, essentially nickel, cobalt and copper. Recyclers are also gearing up to recover lithium, not because it is profitable, but because the EU will mandate that soon.
GH: I agree; the current focus is on high-value materials recovery. Early on, one of the project’s ambitions was to examine a broader range of materials to recover from the battery, including if we want to be truly circular, low-value materials. We want to ensure that as much of the battery is recycled and about moving away from just recovering materials to recovering materials in a higher value state.
PA: We are some way from recovering all materials in a high-value state commercially, but there are companies in the Far East that are manually taking apart battery cells to recover actual material (not just the cylinders or poaches). No one we have spoken to thinks that process will be attractive in Western economies on the grounds of safety and cost. Trying to automate that and to do it safely and cost-effectively is our aim.
The idea of automating recycling is happening around the globe. I know of serious investment in Germany and Norway, and in Autumn 2019, I was at a plant in China in a warehouse full of heavy-duty robots gearing up to do this dismantling task. Automated recycling is not here yet, but it is definitely on the horizon.
Do you think that the finance for recycling will come from industry, or will it receive some government support?
PA: I think we see something of a partnership approach, with some regulation. For instance, the EU is driving through rules for lithium recycling which will apply to the UK (through the Withdrawal Agreement) as we will want to sell into the European market. Government can mandate that companies use so much reclaimed lithium in their batteries too. In addition, in many parts of the world, governments are putting large amounts of public funding into the primary research, such as the Faraday Institution in the UK, to drive innovation. Europe is investing in its businesses for EVs and batteries to build the industry because it is regarded as a vital step.
GH: Regarding higher value materials recovery, the focus is on industry and the problems that directly affect it. The critical materials challenge is more of a broader systemic challenge that will benefit everyone globally. Even on a national level, it does us no good if the UK has the best critical materials strategy, secures access to all resources, and does a brilliant job of making batteries if the rest of the world does not have access to that resource.
Ultimately, with climate change, and all the challenges it presents, we need everyone to do well at critical materials. There is a national competitiveness element, but there is also an international dimension to it. From an industry perspective, if we could improve the recovery of materials from lithium-ion batteries globally by just 1%, that is transformational in terms of the amount of recovered material.
In March 2021, the University of Birmingham completed installing the new battery testing and storage facilities for the ReLiB project. How will this facility be used?
PA: We have to understand how to deal with end of life batteries safely, and this facility will enable us to do that and have the correct infrastructure. The facility is European Council for Automotive R&D (EUCAR) 7 rated. This means it is impact, fire, and explosion resistant, enabling us to examine batteries (some of which are in a poor condition) under controlled conditions to investigate what is happening in them. We need this kind of infrastructure to develop new processes to recycle safely.
The facility itself is expensive, but it is a research facility, and some of our work has now been spun out into an Innovation UK Smart project. This includes my colleagues, Emma Kendrick and Rob Sommerville, and a UK company that want to set up a facility in or near Birmingham to deal with end of life lithium-ion batteries. We have invented a process that physically separates anode and cathode materials without any chemical processing in shredded end of life lithium batteries. This has a significant potential to make downstream recycling processes cleaner and more sustainable.
Finally, what does success look like for the ReLiB project?
PA: It looks like a lot of different things. We are a research project, and we are committed to doing research that is relevant and will roll out to companies. As I just mentioned, the project has three patents, and we have built up IP that can be commercialised. We take our role seriously as innovators to speed up the introduction, not just of recycling 1.0, but recycling 2.0 and 3.0 in the future.
The papers that we have mentioned here create a distinctive idea of what recycling needs to be and where it needs to go. We are in discussions with countries around the globe to bring thought leadership on recycling, and our industrial outputs are critical. Nevertheless, we are not a narrowly focused research project, like several funded through Innovate UK. I view us as a technology pipeline, a kind of ideas factory that keeps analysing the problem and produces better ways to recycle and accelerate progress for the UK, but also, if we are successful, to be taken up globally.
References
- Global implications of the EU Battery Regulation
- The Gigafactory Boom
- The importance of design in lithium-ion battery recycling – a critical review
- Securing Technology-Critical Metals for Britain
- Battery strategy goes flat: Net-zero target at risk
- Risk management over the life cycle of lithium-ion batteries in electric vehicles
Professor Paul Anderson
Professor of Strategic Elements and
Materials Sustainability
Co-Director of the Birmingham Centre for Strategic Elements and Critical Materials
Principal Investigator — ReLiB Faraday Institution project
Dr Gavin Harper
Faraday Institution Research Fellow
School of Physics and Astronomy
University of Birmingham
p.a.anderson@bham.ac.uk
g.d.j.harper@bham.ac.uk
Tweet @unibirmingham
www.birmingham.ac.uk/research/energy/
research/centre-strategic-elements-critical-materials/future-of-batteries/recycling-lithium-
ion-batteries.aspx
Please note, this article will also appear in the seventh edition of our quarterly publication.