The Innovation News Network bring you everything you need to know about the EV battery supply chain, including an in-depth analysis of each aspect of the supply chain, its challenges, regulations, technological innovations, future outlook, and much more.
The automotive industry is undergoing one of the most dramatic transformations in its history. A key element of this transformation is the move towards electric vehicle (EV) technology, driving a global shift to electrification and prompting major changes throughout the EV battery supply chain. This article provides an overview of the current state of the global EV battery supply chain, highlighting recent developments and potential future trends that may shape the landscape going forward.
To understand how this rapidly evolving sector operates, it is necessary to explore all aspects of the global EV battery supply chain, from raw materials sourcing through production and shipping to end-use applications such as consumer vehicles or energy storage systems. It will also discuss regulatory policies related to EVs and their batteries, along with technological advancements that are helping drive down costs and increase efficiency across the entire value chain.
We will examine some of the challenges stakeholders face in managing these new technologies within their organisations and consider solutions for addressing them. By exploring each aspect of the global EV battery supply chain, readers will gain valuable insight into what makes this increasingly important sector tick and how they can best prepare for future requirements.
Overview of the global automotive market
The global automotive industry is an important contributor to economic growth, with strong links to the manufacturing sector. It has become one of the largest employers in many countries and a major source of income. The industry includes components such as engines, transmissions, brakes and other parts used in cars and trucks. In addition, it also encompasses services related to vehicle maintenance and repair, research and development (R&D), transportation infrastructure, retail sales, and marketing.
In recent years, the automotive market has shifted toward electrified vehicles, driven by government policies on emissions reduction targets. This has created a demand for electric batteries which power these vehicles. Battery technology has evolved significantly over the past decade leading to improved energy density and cost reductions. As a result, there is increased interest in expanding electric battery production capacity globally.
This growing demand for batteries presents opportunities for companies involved in the supply chain, from raw materials suppliers to end-user manufacturers. Companies must develop efficient strategies to ensure the reliable sourcing of critical components while meeting customer requirements at competitive prices.
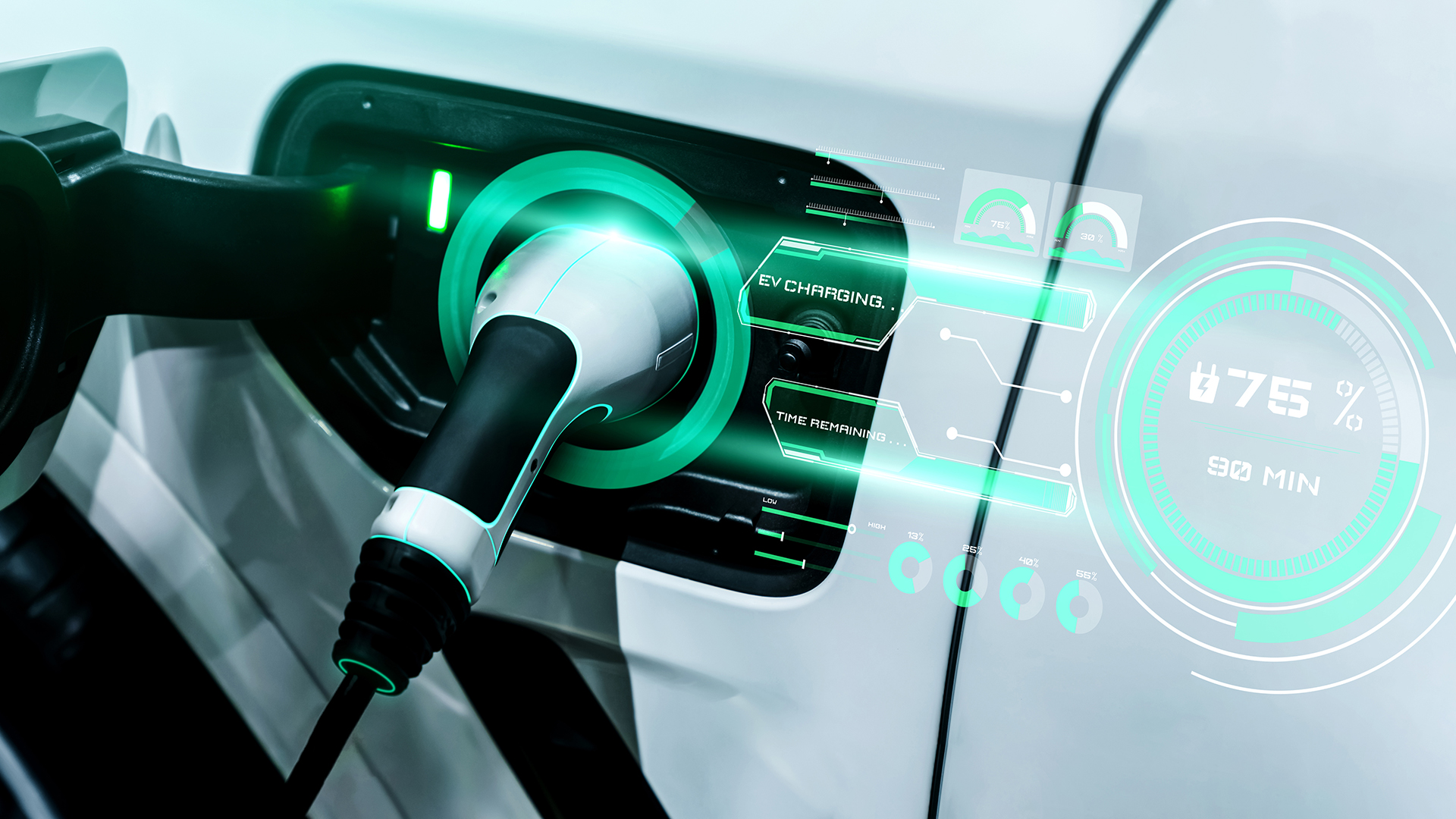
Components of the electric vehicle battery supply chain
The EV battery supply chain consists of components that must be managed for the entire system to operate efficiently. These components include raw materials, production processes, distribution networks, and end-use applications. Raw materials are necessary for making batteries; these can include lithium, cobalt, manganese, nickel and other metals. Production processes involve assembling the parts into a functional whole, including constructing cells and modules and integrating them with electronics and control systems. Distribution networks are required to transport the finished product from manufacturer to customer; this may involve air or ground shipping services depending on geography and demand. Finally, end-use applications must also be managed effectively so that customers receive optimal performance from their vehicles’ batteries over time.
Efficient management of all these components is essential for providing reliable delivery of high-quality products at competitive prices. Achieving this goal requires strategic planning about which elements should be outsourced versus handled internally by each company within the supply chain network. This involves considering factors such as cost-effectiveness, speed of delivery, safety regulations compliance, environmental protection considerations and more. Additionally, it is important to consider how various elements interact with one another to ensure that problems do not arise further down the line due to unforeseen issues related to logistics or compatibility between different parts used during assembly.
Ultimately successful management of an EV battery supply chain depends on having accurate information about every aspect along its length – from material sourcing through production testing and eventually sale and installation in the marketplace – to identify any potential weaknesses before they become serious problems requiring costly solutions.
Challenges in developing an EV battery supply chain
The development of an EV battery supply chain is not without its challenges. These can be divided into three main categories: financial, technological, and logistical.
Financial Challenges
Batteries are expensive components and must be managed carefully for the entire EV supply chain to remain cost-effective. This may include looking for ways to reduce costs on raw materials or finding new funding sources such as government subsidies or tax breaks.
However, finding the necessary funds to develop a supply chain can be difficult. Potential investors must be convinced that the project is viable and that returns will eventually come in.
Technological challenges
The technology used in batteries needs to keep up with the demands of EVs; this means developing more efficient cells capable of storing energy at higher capacities while maintaining safety standards. It also requires keeping up with advances in charging infrastructure and other related technologies, such as fast chargers and wireless power transfer systems.
Ensuring compatibility between different types of batteries and their associated chargers is another challenge that must be addressed when creating a successful EV battery supply chain. It is essential that both hardware and software work together harmoniously so as not to impede progress or cause delays due to incompatibilities.
Logistical challenges
The cost of transporting batteries from one location to another can significantly increase operational expenses if it isn’t done efficiently. Companies need to consider factors such as route optimisation, fuel consumption, loading/unloading time, etc., to minimise transportation costs.
Another major challenge involves ensuring the security of each link within the EV battery supply chain to mitigate any potential risks involved with theft or counterfeiting activities during transit or storage. This includes implementing proper tracking systems, authentication protocols, and encryption measures wherever applicable.
Overall, developing an efficient EV battery supply chain requires careful consideration of various technical, financial and logistical aspects which could affect the system’s overall functioning over time. With these key considerations taken into account before implementation, companies can ensure they create a robust and reliable network capable of meeting current market demands while staying competitive long-term
The role of manufacturers in the supply chain
Manufacturers play an important role in the EV battery supply chain. According to a recent report by BNEF, global production of lithium-ion batteries is expected to reach one terawatt hour (TWh) per year by 2030—increasing from 0.24 TWh produced in 2019. This highlights the need for manufacturers to develop efficient strategies and processes to meet this growing demand.
In terms of raw materials, suppliers source cobalt, graphite, nickel, and other metals used for cathode and anode materials from various mines around the world. The cost of these materials can be volatile due to geopolitical factors that could affect their availability or pricing. Manufacturers must therefore have contingency plans in place when it comes to procuring these raw materials. They should also consider recycling technologies as another way to reduce costs while reducing environmental impacts associated with sourcing new material inputs.
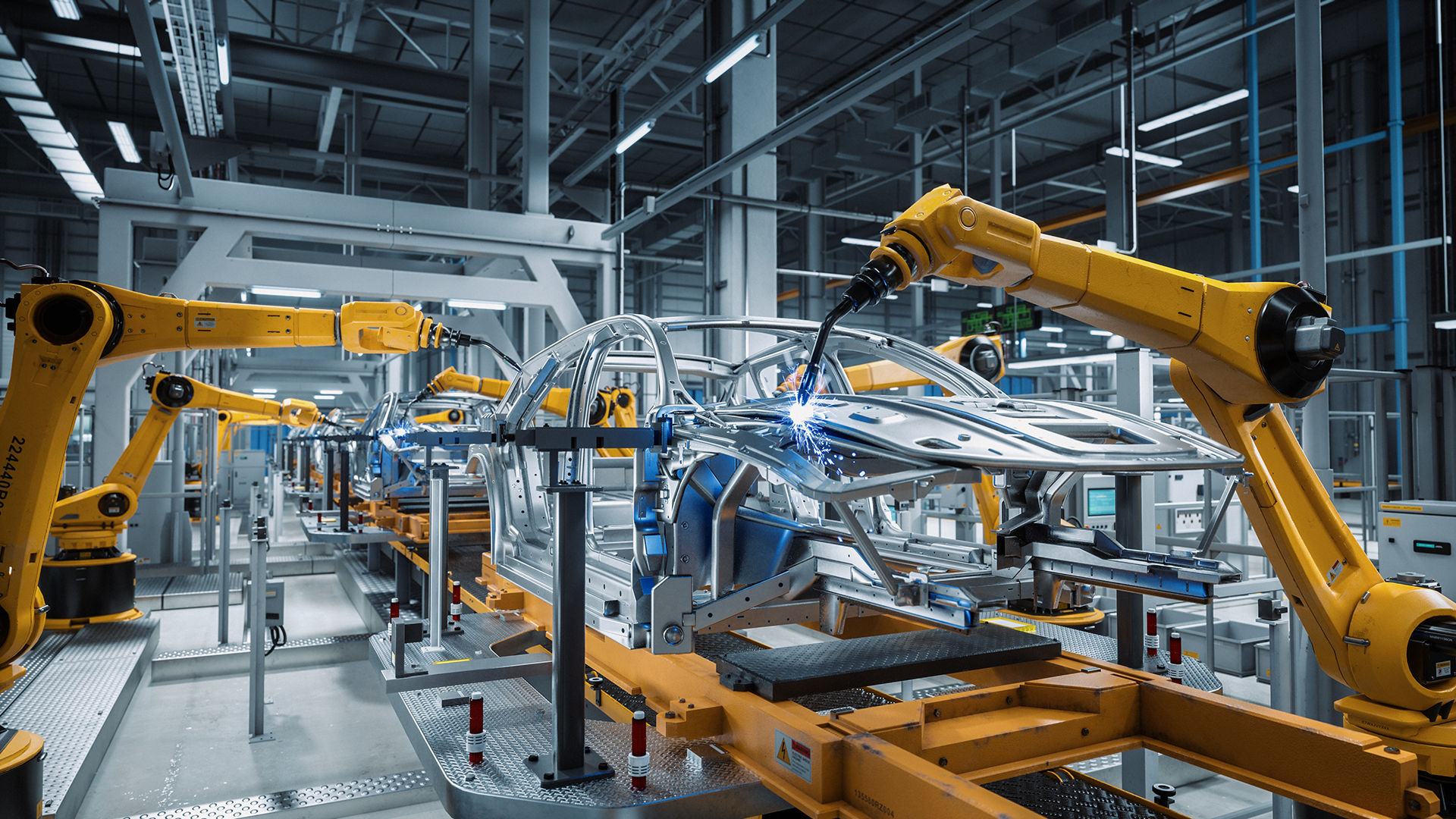
Manufacturers are also responsible for assembling cells into battery packs based on customer requirements; some companies may even design custom solutions tailored specifically for certain applications or customers’ needs. They must ensure that quality standards are met during each process step to avoid potential safety issues further down the line, such as thermal runaway events or fires caused by faulty components during the operation stage. In addition, testing protocols should be followed rigorously throughout development stages to guarantee optimal performance when deployed at scale.
The role of logistics companies
Logistics companies play a critical role in the global EV battery supply chain. They are responsible for transporting goods and materials, ensuring efficient delivery of raw materials to manufacturers and finished products to end customers. Logistics can also help optimise inventory levels within the supply chain, reducing costs associated with overstocking or stockouts. Additionally, logistics companies provide visibility into shipment tracking and real-time communication between stakeholders along the entire route from production to customer delivery.
An effective logistical network is key to maintaining operational efficiency throughout an EV battery’s life cycle. By establishing reliable relationships with multiple suppliers, logistics companies can ensure the timely availability of parts and components manufacturers need while minimising delays due to issues such as port congestion or delayed shipments. Furthermore, they can leverage advanced analytics tools to forecast demand accurately and identify potential risks that could affect performance down the line.
Moreover, logistics providers must develop innovative methods for storing and transporting components safely, so their quality remains intact until they reach their destination. This includes implementing temperature control systems during transit and utilising protective packaging designs to prevent damage caused by shock or vibration during shipping. Companies often partner with third-party service providers specialising in hazardous material handling and storage solutions if dangerous chemicals are shipped along the EV battery supply chain. By taking these measures, logistics companies can reduce bottlenecks in the supply chain flow and improve overall customer satisfaction rates.
How tech companies impact the supply chain
It may seem that tech companies have no role in the EV supply chain, but this is not necessarily true. Tech companies can partner with EV manufacturers and suppliers to provide a range of services aimed at improving customer experience and satisfaction. For example, tech giants such as Google and Microsoft work with EV manufacturers on software development for autonomous driving applications or AI-enabled dashboards. These collaborations create opportunities for greater efficiency and accuracy throughout the entire EV supply chain, from production to distribution.
In addition, tech companies can also serve an important role in providing insights into consumer buying patterns. Through the use of analytics tools, they can collect data about customers’ preferences regarding features, design and safety, which could help inform decisions made by EV manufacturers during the product design process. This ultimately leads to improved quality control measures and better customer experiences when compared with traditional combustion engine vehicles.
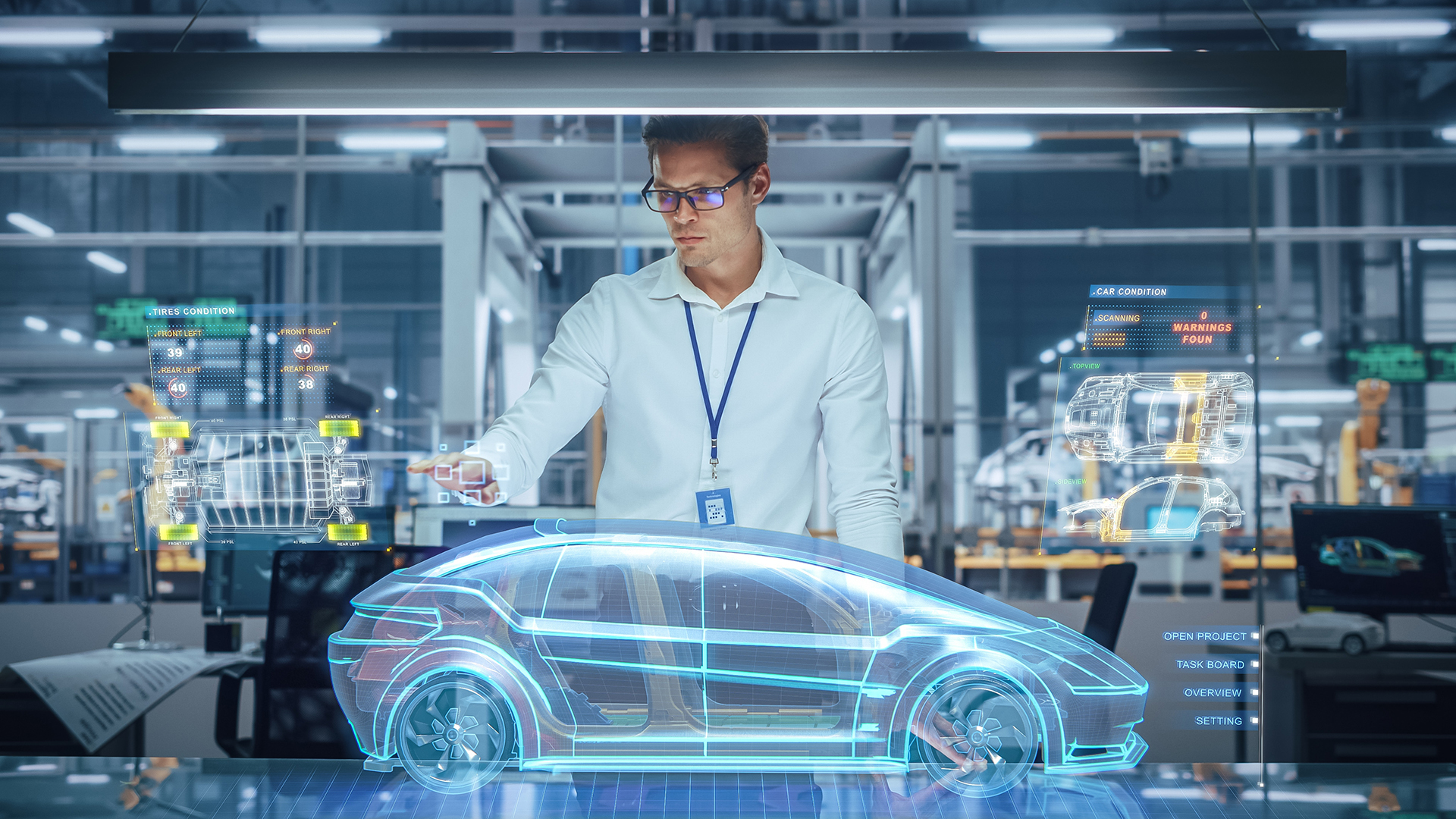
Tech firms are also increasingly involved in developing innovative solutions related to battery technology which has implications for cost savings and performance improvements within the EV sector. Solutions such as cloud-based battery management systems allow EVs to be more efficient while reducing the need for costly onsite maintenance visits, resulting in lower operational costs over time. Additionally, these advances will enable faster charging times, leading to improved convenience for drivers while reducing emissions associated with long waiting periods at charging stations.
The impact of regulations on the EV supply chain
The impact of regulations on the global EV battery supply chain is significant. Regulations affect both manufacturers and consumers alike, as well as local governments. Governments worldwide are increasingly enacting laws that affect how electric vehicles are produced, sold, and used. This has led to changes in how batteries are sourced, manufactured, tested, transported, and stored.
Examples of recent regulations include:
- Manufacturers must adhere to strict emissions standards when producing EVs;
- Consumers may be eligible for tax credits or subsidies when purchasing electric cars;
- Local governments can impose restrictions on where EVs can be charged; and
- Many countries have adopted zero-emission targets to reduce their dependence on fossil fuels.
Regulatory measures such as these incentivise companies to develop new technologies and innovate to meet environmental goals set by governments. They also create a level playing field among competitors regarding allowable production levels and other requirements that must be met before hitting the market. Ultimately, this leads to greater competition between producers and improved quality control procedures across the entire supply chain.
Financing options for establishing an EV battery supply chain
The financial requirements for setting up an EV battery supply chain can be significant, depending on the size and scope of the project. Financing options are available to potential investors who wish to embark upon such a venture. Debt financing is one option that may be attractive due to its relative cost-effectiveness. This type of financing entails borrowing money from lenders such as banks or other institutions at a predetermined interest rate with repayment terms agreed upon in advance. Equity financing involves raising funds by selling ownership shares in the company to investors; this method has no associated debt obligations but also carries a higher risk than debt financing.
Tax incentives may also be available when setting up an EV battery supply chain business, making it more feasible financially. Incentives can range from local tax credits or subsidies to national programmes offering reduced taxes or grants for start-up capital and research & development expenses. Furthermore, governments worldwide have implemented various green energy initiatives which offer additional benefits such as preferential electricity tariffs and access to low-cost loans for renewable energy projects. These incentives help reduce upfront costs and increase profitability over time, making them especially attractive for businesses considering investing in an EV battery supply chain business model.
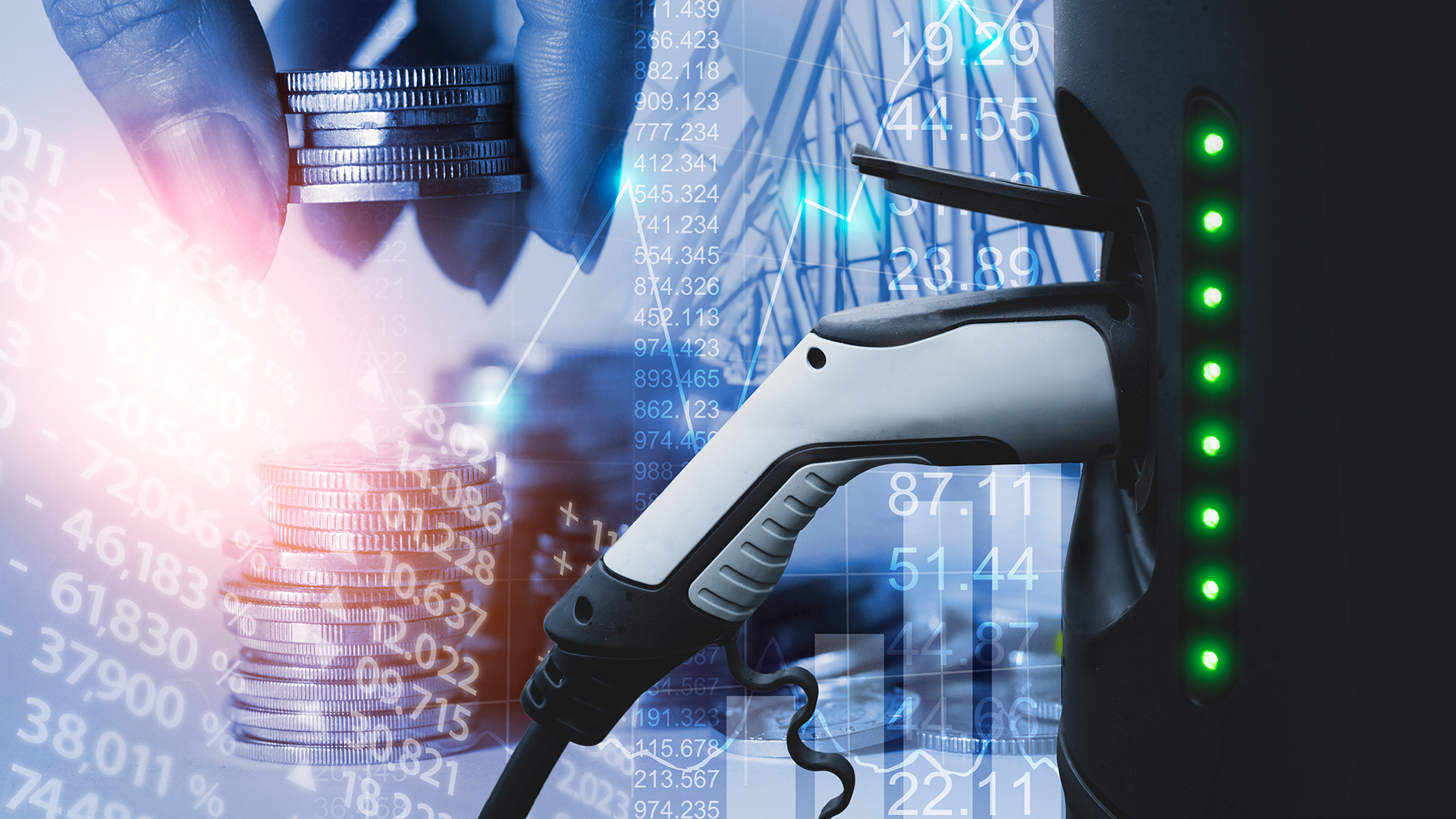
Given these considerations, there is a wide variety of financing options available for those wishing to establish an EV battery supply chain operation. Careful assessment of each option should be conducted before committing any resources towards a particular approach; this will ensure that the most suitable choice is based on individual needs and circumstances.
Latest supply chain innovations and trends
Recently, the global EV battery supply chain has seen exponential growth in demand due to the increasing number of people adopting this technology. According to a report by BloombergNEF, global EV sales rose 50% year-on-year in 2020 and are projected to keep growing rapidly. This surge in demand has led to several innovations and trends within the industry that have made it possible for manufacturers to produce high-quality batteries at lower costs.
Here are three key advancements and trends that are shaping the future of the global EV battery supply chain:
- Energy Density Improvement: Battery energy density is one of the most important criteria for evaluating EVs, as higher energy density contributes to increased range per charge. Significant advancements have been made in improving the energy density of Li-ion cells over recent years. Innovations such as using nanomaterials, solid electrolyte separators, etc., allow greater storage capacity with smaller sizes making them more efficient;
- Cost Reduction: With rising demand from automakers around the world, there have been numerous measures taken towards reducing production costs without compromising on safety standards or performance levels. Automakers now use new technologies such as automated production lines, which reduce labour costs while allowing faster assembly times, resulting in lower prices for consumers; and
- Environmental Sustainability: Manufacturers across all industries increasingly focus on sustainability initiatives, including green manufacturing processes and responsible disposal methods to reduce carbon footprints and protect our planet’s resources. In particular, companies producing EV batteries are exploring ways to recycle used lithium-ion batteries instead of disposing of them, thus minimising environmental damage caused by toxic waste products generated during manufacture.
Overall, these technological improvements and business strategies offer great opportunities for companies operating within this space, enabling them to stay ahead amidst stiff competition while also helping expand access to clean transportation solutions globally through reduced pricing options and improved product efficiency
Emerging technologies driving change in the industry
Advances in technology have enabled significant changes to the EV battery supply chain. Automation, robotics and digitalisation are all being integrated into the production process, resulting in improved efficiency, cost savings and enhanced safety standards. Robotics can reduce costs by automating repetitive tasks such as material handling, packaging and assembly line operations. Digital tools can also provide companies with real-time access to data about their supply chains that allow for more informed decisions regarding resource allocation and inventory management. Furthermore, blockchain technology is now being utilised to improve visibility across the entire value chain, from raw materials sourcing to final deliveries of batteries. This allows businesses to gain greater control over their processes while simultaneously improving traceability and transparency.
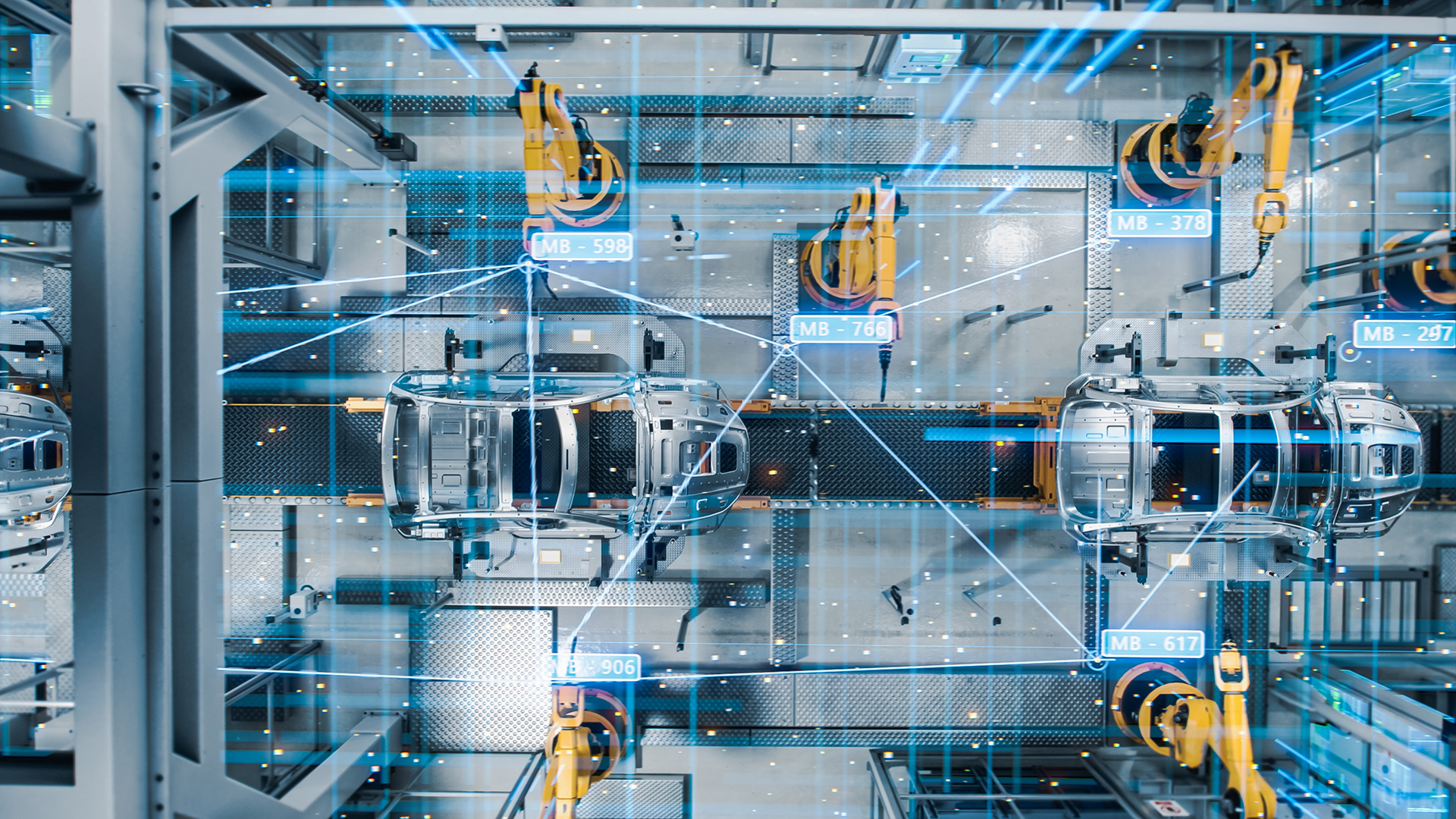
The introduction of AI has further facilitated advancements in the EV battery supply chain by allowing machines to make autonomous decisions about product selection or production scheduling without direct human supervision. AI algorithms can detect patterns in large datasets, enabling better predictive analytics when it comes to forecasting demand or identifying areas where operational improvements could be made. Additionally, AI-powered robots can automate tedious manual tasks such as quality inspection or sorting parts according to specifications, increasing accuracy while reducing labour costs.
In addition to increasing operational efficiency within factories, new technologies like wireless connectivity are increasing collaboration between manufacturers and other parties involved in the EV battery supply chain – suppliers, distributors and customers alike. By sharing data securely on a single platform, they can streamline communications while having access to near real-time information regarding inventory levels, pricing trends or delivery updates leading to an improvement in overall customer service experiences.
EV battery supply chain best practices
To maximise efficiency and ensure a successful EV battery supply chain, several best practices should be followed. First, companies need to develop an accurate understanding of the demands of their customers to provide the most appropriate solutions. Companies must also understand the needs of their suppliers in terms of materials and labour resources so they can negotiate fair prices and timely delivery. Also, establishing strong relationships with internal stakeholders, such as employees, and external partners like vendors is essential.
Companies must have a clear plan when transitioning from traditional technologies to emerging ones in the EV battery supply chain. This includes having a thorough evaluation process which identifies areas where improvements could be made, developing strategies for achieving these goals, and monitoring progress throughout the transition period. Access to reliable data about customer demand, industry trends, and production costs will help inform decisions.
Successfully managing all aspects of a global EV battery supply chain requires investment in training personnel on new systems or processes and maintaining adequate communication among team members across different geographic locations. By following these best practices, organisations can create efficient operations that meet customer needs while controlling costs and minimising disruption caused by technological changes.
Strategies for optimising performance
Optimising performance in the EV battery supply chain is paramount to its success. The ever-increasing demand for electric vehicles, their components and batteries necessitates efficient strategies that optimise production and cost-effectiveness. Astonishingly, several innovative approaches to streamlining operations in the global EV battery supply chain exist.
Firstly, manufacturers should implement Industry 4.0 principles such as automation and data analytics to reduce costs while increasing efficiency. Automation could be used throughout manufacturing stages, from material handling to assembly line robotics; this would prevent human errors and optimise resource utilisation. Furthermore, predictive analytics can provide insights into which products will be most profitable or require more resources before production commences.
Secondly, suppliers should consider digitalising their entire supply chain process using technologies like blockchain or the Internet of Things (IoT). This would enable real-time tracking of materials and enhanced visibility over every step of the process – allowing companies to anticipate any potential issues before they arise. Additionally, implementing distributed ledger technology (DLT) solutions would ensure secure and transparent communication between all stakeholders while simultaneously providing greater transparency regarding product quality across multiple parts of the value chain.
Finally, effective collaboration among all players in the industry is essential for a successful EV battery supply chain strategy since it allows companies to optimise procurement cycles by taking advantage of economies of scale produced through larger orders, thereby reducing risks associated with price fluctuations due to market volatility and ensuring timely delivery at competitive prices.
To maximise profits and achieve optimal performance within the global EV battery supply chain, manufacturers must embrace new technological advancements made available today while fostering relationships with other members of their ecosystem – creating an environment where everyone wins
Essential cost considerations
Optimising EV battery supply chain performance involves numerous considerations, including cost. The costs associated with an evolved EV battery supply chain can be significant and must be managed carefully to ensure success. Analysing current and projected expenses is essential for evaluating the potential return on investment when optimising the supply chain.
An effective way to manage costs within an optimised EV battery supply chain is to identify areas where resources are wasted or overused. For example, if a company is spending too much money on storage space, it can use that capital instead to invest in new technology or services that could improve its overall efficiency. Additionally, companies should consider exploring alternative suppliers who may offer more competitive rates than existing ones. By finding ways to reduce costs while still maintaining quality standards, businesses can maximise their budgets while improving their bottom line.
It is also important to determine what strategies are most suitable for managing costs across different stages of the supply chain process. This includes understanding factors such as how long it takes from order placement until delivery; analysing transportation methods available and determining which will provide the best value for money; assessing inventory management systems used by various organisations; and developing distribution networks that deliver products at minimal expense. All these elements need special attention when attempting to control costs throughout the entire supply chain process successfully.
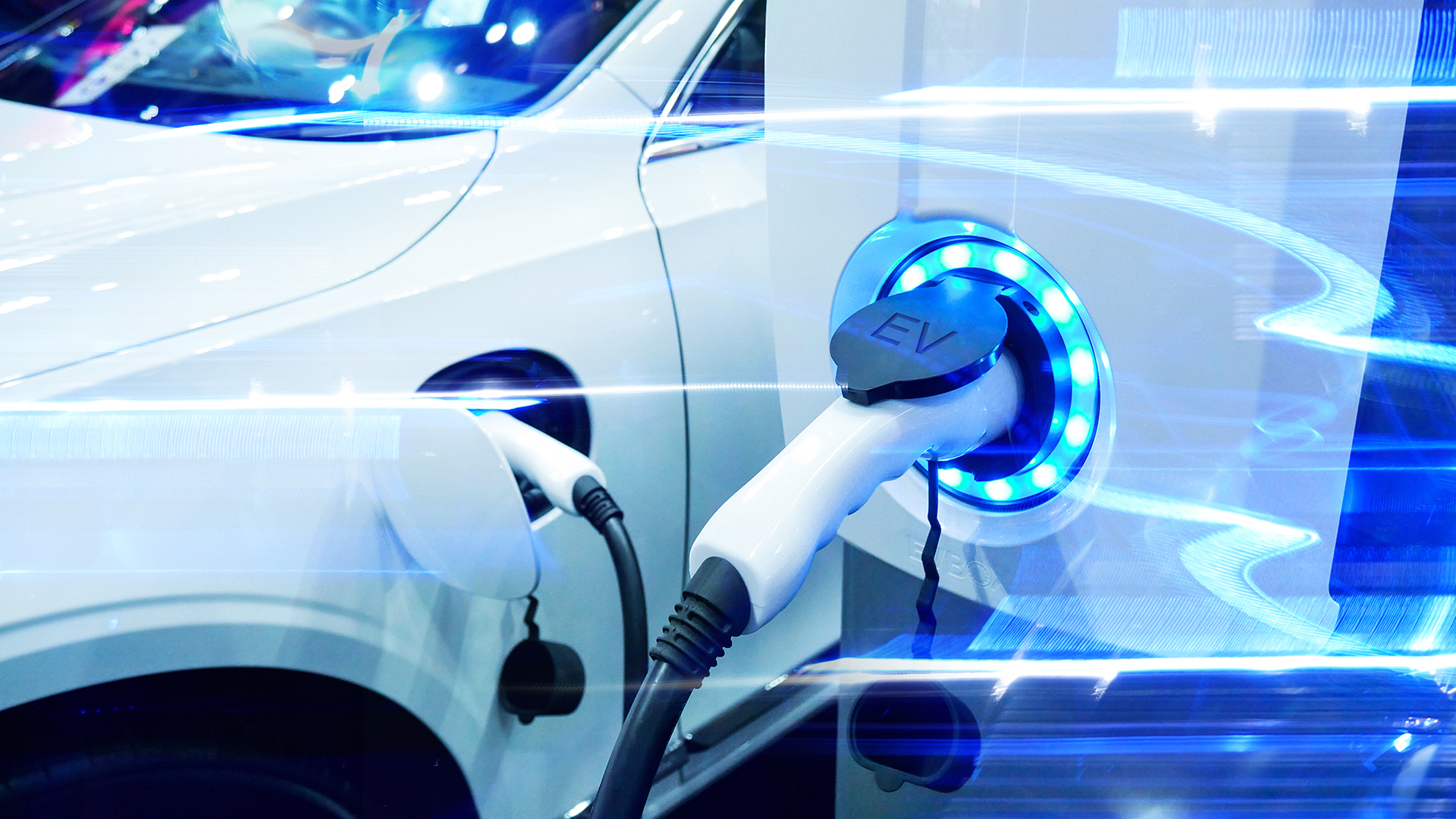
To achieve optimal results from cost-management efforts, having a clear strategy in place outlining operational goals and objectives is pivotal. Companies should set measurable targets for areas such as supplier performance and customer satisfaction levels alongside financial objectives so that any efficiencies made can be tracked and assessed against predetermined criteria. In addition, regular reviews of organisational processes should be conducted along with benchmarking studies to measure progress towards achieving stated objectives related to cost reduction and improved profitability.
Benefits of investing in a robust global EV battery supply chain
Investing in a robust global EV battery supply chain can provide numerous benefits to the automotive industry. According to research conducted by Frost & Sullivan, electric vehicle sales are expected to exceed eight million units worldwide by 2030. This surge in EV demand has created an opportunity for automakers and suppliers alike to capitalise on this growing market through investments in their respective battery supply chains. By doing so, these companies could take advantage of several potential benefits that could help them stay ahead of their competition.
The first benefit is increased efficiency across the entire value chain of the automobile industry. As most manufacturers have extended production times due to the limited availability of batteries, investing in a reliable and well-developed supply chain could reduce such delays significantly. A well-integrated network of suppliers would allow automakers to respond better quickly and effectively when faced with unexpected changes in consumer demand or technology advancements. Additionally, they would be able to manage inventory levels that could potentially lead to significant cost savings over time.
Another benefit is improved customer satisfaction rates, ultimately resulting in higher sales figures and greater brand loyalty among consumers. Customers today expect their vehicles delivered within a certain timeframe; having access to reliable batteries ensures they will receive their cars as promised without any additional wait times. Furthermore, customers also appreciate being kept informed about their order status throughout each stage of the process; efficiently managing communication between stakeholders involved in the supply chain helps ensure smooth transaction experiences.
In addition to providing operational advantages, investments into global EV battery supply chains also offer strategic opportunities for organisations looking for new sources of revenue growth or other competitive advantages. Automakers and suppliers who invest early could gain an edge against those who don’t since they’ll already have established relationships with key players along the value chain before anyone else does. Such partnerships may lead to exclusive deals or shared knowledge that puts them at an even further advantage than traditional competitors in the auto space.
Future outlook For the sector
Looking to the future, a robust global EV battery supply chain and its associated investments have the potential to create long-term economic value as well as environmental benefits. For these advantages to be realised, there are several necessary steps that must be taken to ensure the growth of this industry. These include increasing research and development into more efficient production methods, encouraging investment in both public and private EV infrastructure projects, and providing incentives for manufacturers of EV batteries.
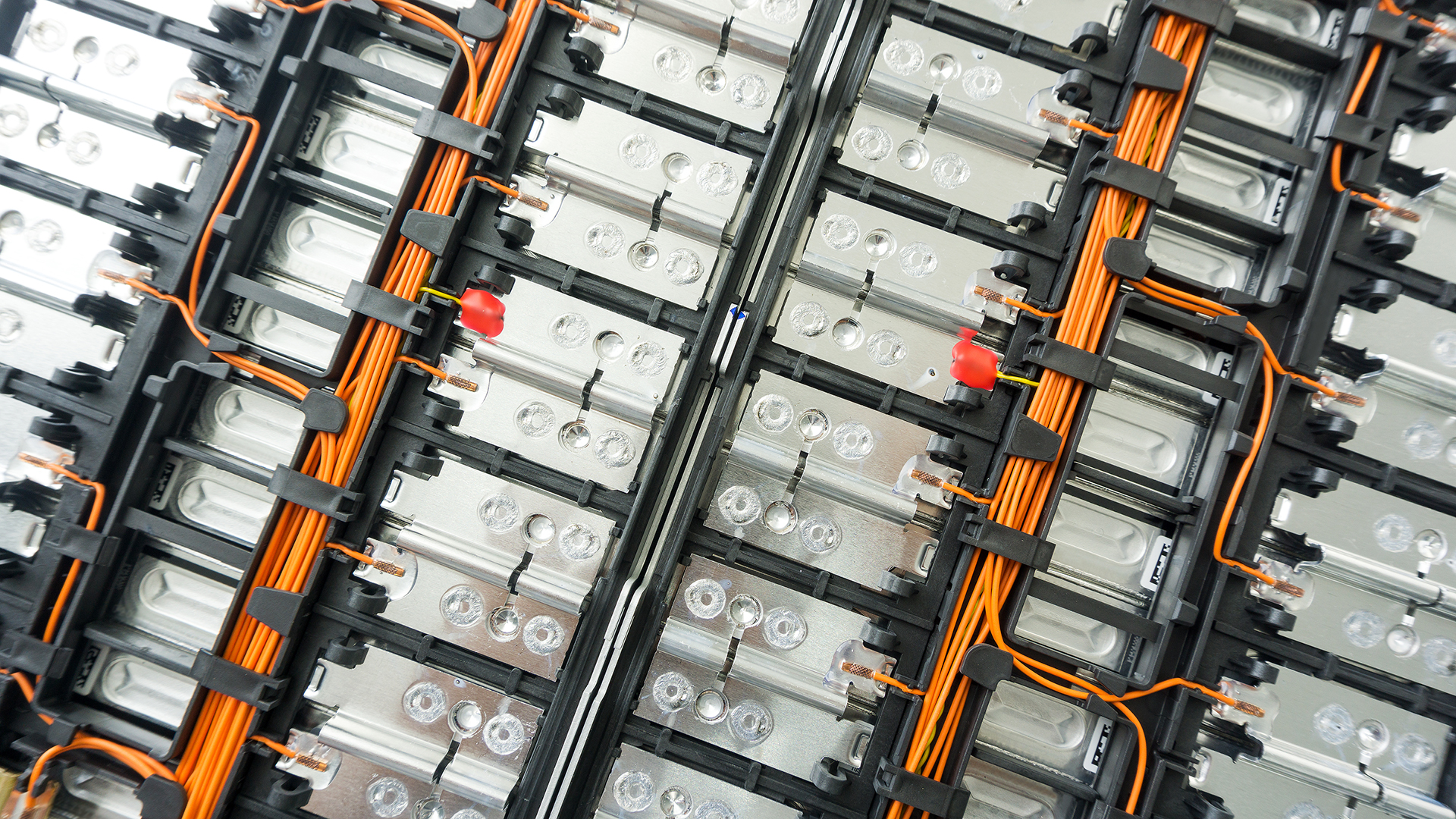
The continued implementation of government initiatives designed to support the growth of electric vehicles will play an integral role in sustaining a robust global EV battery supply chain. Such initiatives may focus on creating attractive financial incentives, such as subsidies or tax breaks, while also developing standards for safety regulations and quality control measures. Additionally, governments could fund research activities related to advanced technologies, such as new materials and chemistries that can improve battery performance over current models. This type of activity would help accelerate the adoption rate by making EVs more affordable and reliable for consumers.
As consumer demand continues to increase, further innovation will likely come from both existing suppliers within the EV battery space as well as emerging players who seek to capitalise on the growing market opportunity. With increased competition comes opportunities for improved efficiency gains through economies of scale, leading to lower costs which should benefit consumers further down the line. Thus, with appropriate policy support and sustained investment in R&D efforts across different areas of technology involved with producing EV batteries, it is expected that a strong global EV battery supply chain will remain viable far into the future.
Investing in a robust global EV battery supply chain will bring numerous benefits to the automotive industry. The challenges presented by these supply chains are immense, but with careful planning and execution, these can be overcome. With manufacturers recognising their role in developing reliable supply chains, as well as logistics companies taking steps to optimise performance, it seems that an evolved EV battery supply chain may soon become a reality. Furthermore, cost considerations have been considered when assessing potential solutions for this difficult problem.
The evidence points towards a future of seamless global EV battery supply chains that result in greater efficiency throughout the entire automotive market. As technology advances and innovation accelerates at an unprecedented rate, we may see even more improvements within the next few years. In fact, some experts believe that electric vehicle batteries could soon revolutionise transportation altogether!
Ultimately, investing in a global EV battery supply chain has the potential to completely transform how cars are produced and distributed on a worldwide scale – providing better access to clean energy sources for both consumers and businesses alike. This would tremendously impact our environment and economy while creating new opportunities for those involved in all aspects of the industry.