With industries globally taking imminent measures to curb emissions, we explore the strategies that must be implemented to create a green magnesium production sector.
Magnesium, one of the most abundant elements in the Earth’s crust, is a lightweight and versatile metal with applications ranging from aircraft construction, electric vehicles (EVs), and beverage cans.
Yet, bringing this seemingly innocuous metal to market carries a hidden cost: greenhouse gas emissions. Understanding these emissions, their sources, and potential mitigation strategies is crucial as we strive for a more sustainable future for the magnesium industry.
The power-hungry magnesium production process
The primary method of magnesium production, the electrolytic process, requires substantial energy, primarily in the form of electricity.
This results in significant carbon dioxide (CO2) emissions, depending on the source of electricity. In China, which accounts for approximately 77% of global magnesium production, reliance on coal-fired power plants leads to high emissions, with estimates ranging from 19 to 28 kg CO2-equivalent per kg of magnesium produced.
Additionally, the Pidgeon process, an alternative method still used in some regions, utilises carbon-based reductants like coal or coke, further contributing to CO2 emissions.
Research suggests that optimising energy efficiency and transitioning to renewable energy sources in magnesium production are essential for reducing CO2 footprint.
Embracing the circular economy: Recycling and beyond
Fortunately, magnesium boasts strong recyclability characteristics. Reusing scrap magnesium requires only 5-10% of the energy needed for primary production, significantly reducing emissions.
This makes fostering a robust magnesium recycling infrastructure a crucial step toward a more sustainable industry.
Furthermore, research into novel magnesium production methods, such as extracting magnesium from seawater or using bio-based processes, holds promise for further emission reductions.
Investing in these technologies and exploring cleaner alternatives to both the electrolytic and Pidgeon processes can pave the way for a greener future for magnesium production.
Al-thermic Process: A true green alternative for magnesium production
Among all the emission-cutting initiatives across the magnesium production landscape, one stands above all in terms of sustainability – the Al-thermic Process.
MFE Magnesium For Europe GmbH is now championing the Aluminothermic (Al-thermic) Process to reduce industry emissions across Europe.
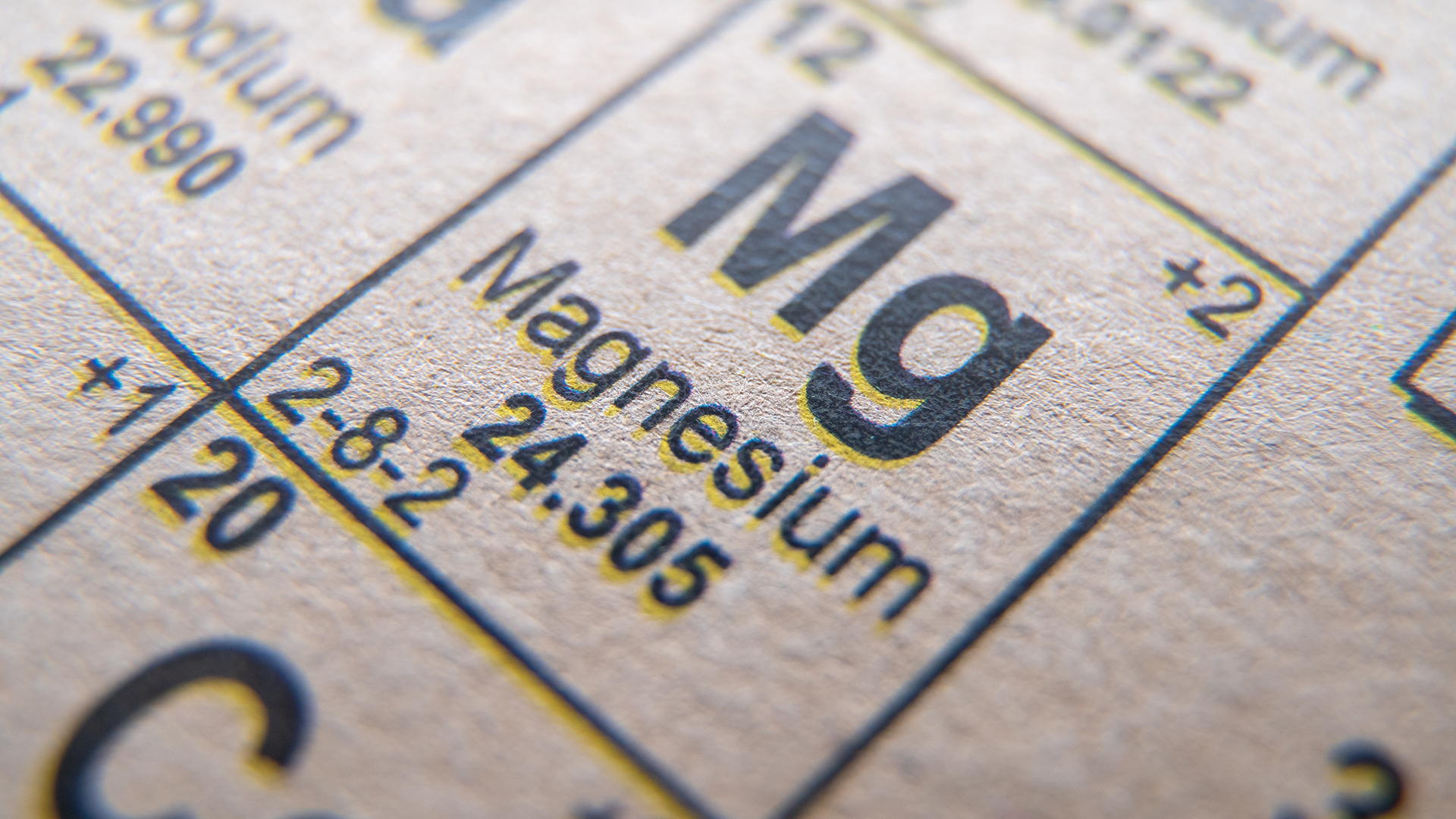
The Al-thermic Process stands as a noteworthy advancement in magnesium extraction methodologies, notably surpassing traditional techniques such as the longstanding Pidgeon Process and the Magnetherm Process.
Utilising FerroSilicon in a vacuum at high temperatures for magnesium extraction from dolomite, the Pidgeon Process held its ground as the industry standard for over five decades, particularly in China.
However, criticism has mounted against this approach due to its excessive energy consumption, substantial CO2 emissions—especially when powered by coal-generated electricity—and the production of waste slag.
In response to the escalating global awareness of climate change and increased scrutiny of industrial processes, China, a predominant magnesium producer, reevaluated its production methods to align with new CO2 reduction targets.
This reassessment led to the inception of the Al-thermic Process, which builds upon established technology but introduces three pivotal modifications:
- Post-calcination of dolomite, Ca-Mg separation enables the production of PCC (CaCO3) and Dry Ice;
- The use of Al or Al-scrap as a reductant replaces FerroSilicon, resulting in the production of Al-Mg-Spinel and a zero-waste process; and
- Operating at a lower temperature of 1150°C contributes to a more energy-efficient process.
The Al-thermic Process not only extracts magnesium but also yields three valuable by-products—PCC, Dry Ice, and Al-Mg-Spinel—while generating zero waste. The process also generates high-quality raw materials to manufacture a range of products.
This innovation aligns with global initiatives to reduce the environmental impact of industrial processes, representing a substantial stride toward sustainable magnesium production.
A call to action
Global magnesium production emissions deserve our attention. Numerous avenues exist to mitigate this hidden environmental burden.
Embracing these solutions and fostering innovation is not merely an option, but a responsibility for a truly sustainable future.