True 2 Materials’ state-of-the-art material recovery from end-of-life and production scrap EV batteries will ensure a competitive EV supply chain.
Global transportation markets are undergoing rapid change. We are seeing many companies involved in the transition from internal combustion engine (ICE) to electric vehicles (EVs) expanding into areas outside their traditional or core expertise. Car companies are getting into mining, and mining companies are planning on making battery cathodes or placing bets on recycling companies. Industries are expanding their scope because the marketplace has changed more rapidly than ever in the last 100 years.
A competitive advantage in EV supply chains is paramount to winning going forward. The best way to assert control over the strained materials supply is through state-of-the-art material recovery from end-of-life and production scrap EV batteries. True 2 Materials’ approach is known as Total Material Recovery (TMR).
How does TMR differ from traditional battery recycling methods?
TMR is a break from traditional recycling methods, which are themselves derived from old mining processes. There are a few ways to recycle end-of-life EV batteries and production scrap, and a handful of well-funded companies are vying for leadership in this relatively new market. We often read about the varying degrees of metal recovery, the innovation, and the pedigree of their principles.
Hundreds of articles explain how solving waste and end-of-life battery recycling can make for a profitable and cleaner EV supply chain. We indeed share this vision but are left with questions about how these companies will address recycling cleanly while preserving maximum value at minimum cost, especially when all environmental costs are fully priced. How much innovation is possible when discussing hydro and pyrometallurgy?
Increasing the value of the EV supply chain
The EV supply chain is in the very early stages, and no one can solve our most significant problems with the toolkit currently available to the leading contenders. Typical media stories do not ask meaningful questions about where we are and where we need to be to succeed as an industry. In order to further the supply chain, they must be addressed.
Media articles typically teach us that batteries are first shredded into black mass and that, from this black mass, valuable metals are extracted, often with success rates at anywhere from 90-95%. But what is in black mass?
Electrolytes make up approximately 20% of black mass. They are not metals, though they can contain small amounts of lithium. Electrolytes are, however, toxic and dangerous to dispose of. So what happens to them in the battery recycling process? Are they recycled at all? That will depend on the method of recycling deployed. As these essential electrolytes cannot be recycled at high temperatures (pyrometallurgical approaches) or with concentrated acids (hydrometallurgical approaches), an entirely new electrolyte removal step must be somehow developed and bolted on to the front, adding complexity and cost to an already complex and expensive procedure. Where is this electrolyte removal process?
Black mass also contains a large amount of graphite. Not just run-of-the-mill graphite but highly processed, high-value, battery-grade graphite. What happens to it? Is it recycled? In some cases, it is burned, and what is lost is counted as recycled as it heads out the exhaust. It can also be turned into low-grade carbon black. How much of it is lost, though, not merely downcycled? We do not know the actual numbers there, but we know there is a better way. Why destroy or downcycle this valuable resource? Estimates are that we need roughly 100 mines to produce enough graphite for future EV demand. There are currently around 20, and nowhere near the 80 potential new mining sites required. Preserving this graphite is essential.
Extensive research has gone into Froth Flotation to recover graphite. However, as another traditional mining technique, froth floatation struggles to reach the strict purity requirements for the materials used in modern battery manufacture. Yields are still poor and the remaining graphite adversely affects metal recovery. It also requires extensive pre-treatment and is difficult to scale at any cost.
TMR is a novel battery recycling approach, and with graphite and other metals entirely separated in the first step, the value preserved is not only in recovered graphite but also in increased recovery yields of the metals. Economically this makes much sense; environmentally, it is essential.
Electrolytes and carbon materials make up more than 50% of typical black mass, so why do battery recyclers talk about metal recovery exclusively? Metals are the most lucrative target for recycling in end-of-life cells, but the costs and shortages of graphite and the environmental challenges electrolytes pose are fundamental problems to solve. From our point of view, destroying value here is unforgivable.
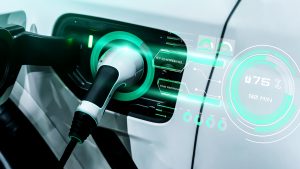
Important questions must be addressed
The EV battery chemistry with the fastest-growing market share is lithium iron phosphate (LFP). With no nickel or cobalt, what exactly are traditional recyclers going to go after? Are the yields going to justify the costs? What kind of subsidies will be necessary to process these batteries? Or will the costs be passed on to original equipment manufacturers (OEMs), and hence finally, the consumers instead?
There is typically more lithium in LFP chemistries, but traditional battery recycling is suboptimal for recovering lithium. We see the can being kicked far down the road regarding this chemistry. The game plan will be a tooth-and-nail battle between recyclers over the lucrative NMC feedstock, with LFP being treated as a junk product.
Total Material Recovery (TMR) is a modern process developed in the 21st Century. Spending billions on building giga-structures for recycling based on technology that is hundreds of years old is a misallocation of capital. We want to start to see articles that pose these three questions to battery recyclers:
- Why do you get your metals back as sulphates instead of oxides, and is downgrading from oxide to sulphate the best solution?
Total Material Recovery recovers all the metals from cells back as oxides.
- What happens to the electrolytes and graphite in the cells you recycle? Are you recovering the expensive spherical graphite in a non-degraded form?
Total Material Recovery recovers all the graphite as it was in the battery; it can be reused. The electrolytes we recover are undegraded. They are safe and offer a pathway to re-use.
- What are your plans for cells made with comparatively low-value materials such as LFP, which are capturing more market share each year? Are you planning on turning a profit from recycling them, even without any cobalt or nickel?
We must push past platitudes and general claims of being chemistry agnostic, doing good for the environment, and making the EV supply chain greener. We need to know how battery recycling impacts the need for battery materials and new mining.
The way to see what is going on is to nail down the costs of processing a given chemistry and compare that with the value recovered. The math is very simple – if the value is being destroyed, you cannot hide it. The cost of materials of an EV cell pack represents about 70% of the money spent as of autumn 2022 (they should be falling with cheaper chemistries coming onstream and lithium prices dropping). A $10,000 battery pack has approximately $7,000 of battery materials inside, but how much of that is earned back and at what cost? If the end product contains carbon black, degraded or missing electrolytes, and only 95% of the non-lithium metals, the numbers will not lie.
The great thing about Total Material Recovery is that recovering metals as high-purity oxides gives one huge flexibility. While our iron oxides could quickly be cycled back into the next generation of batteries, one could also sell them on the spot market should one desire.
We do not plan on LFP battery recycling being a money-losing venture. In addition, while competition will be good for the EV supply chain, realistically True 2 Materials does not need a large scale to hit profitability. Giga structures are optional and undoubtedly not optimal. The recycling industry has overcapacity already after all. When we consider scale for processing production scrap, clearly a smaller footprint will be more economical.
We see the future of recycling requiring better economics, and T2M looks forward to providing solutions to get us all there.
Please note, this article will also appear in the sixteenth edition of our quarterly publication.