The Technological University of the Shannon (TUS) is spearheading several projects designed to transform polluting plastics into a resource for indefinite circularity in tandem with nature.
The wellbeing of the planet and its inhabitants, more than ever before, depends on sustainable innovation to move to circular living. Nature operates a myriad of elegant routes to effectively self-regenerate in a cyclical fashion. This is a template for managing polluting plastics and overcoming the generation of enormous waste stockpiles.
In many economic sectors, the world continues to operate in outdated linear modes, where mined and extracted resources are manufactured as products, which are consumed and then discarded as waste. This scenario is especially pertinent in the case of plastics. The discovery of plastic polymers in the early-to-mid-20th century, and their intense scientific and engineering development in recent decades, has resulted in a ‘wonder material’ with remarkable lightweight, high mechanical performance and a plethora of other desirable properties, such as flexibility, strength, versatile shapes and sizes, and inert stability.
Plastics are now ubiquitous and can be credited with a significant role in recent rapid human progress. Critically, post-use and at end-of-life, plastics are not currently sufficiently revalorised as new products in a continuous use cycle and are instead disposed of as waste with a range of negative environmental consequences. The omission of technology development to complete the life cycle for plastics, combined with the unabated demand for ever increasing production, is a significant factor in the current global environmental crisis.
In Ireland, the drive for sustainable plastics circularity is being spearheaded by the Technological University of the Shannon (TUS), which is known as the country’s home of polymer engineering. With more than 15,000 students in Ireland and an additional 100,000 across its Regional University Network (RUN-EU), TUS has a wide and growing rapport with the plastic value chain industry and its clients. The new Centre for Polymer Sustainability (CPS) at TUS is led by Dr Margaret Brennan Fournet and is dedicated to helping industries achieve sustainability for their products and processes while creating new circular value chains. Its primary focus is the fast-tracking of innovation for how plastics are made, unmade, and remade through a series of radically new technologies. Central to this are a number of collaborative EU projects, primarily BioICEP and EcoPlastiC.
BioICEP: Delivering radically new sustainable plastic technologies
BioICEP (Bio-Innovation of a Circular Economy for Plastics) is a €7m flagship EU-China Horizon 2020 project, which brings together leading experts from industry and academia to build a set of purpose-designed and groundbreaking technologies in order to achieve a Circular Economy for Plastics. The globally successful collaborative team is led by TUS and includes researchers from both the Natural Science Foundation of China (NSFC) and European-based partners.
The ethos of BioICEP is to build technologies that match the natural biomaterial lifecycle for polymers. In the environment, a series of natural lifecycle stages are used to repurpose post-use or end-of-life biomaterials and biopolymers, including familiar structures such as DNA, cells, and polysaccharides. These resource-rich elements are broken down, repurposed and reintegrated as part of new environmentally beneficial materials and beings, such as the nutrients for plants and animals. The food chain is a prime example of this system in action. Top predators digest the meat of animals, which have been sustained from the consumption of vegetation, which in turn grew using nutrients made available by fungal and microbial decomposition and processing of end-of-life flora and fauna biomaterials, as part of a continuous self-sustaining cycle.
By taking guidance from nature, our team of experts are developing new next-generation green technologies to degrade and digest polluting plastics and then regenerate them as new alternative bioplastics. The process begins by using a sequential approach, starting with mechanical/green chemical technologies, which simulate natural weathering and arthropodal dismantling activities. This is followed by accentuated microbial and biocatalytic treatments, to yield effective depolymerised waste plastic feedstocks. Revalorisation using virgin-to-virgin loops, bioprocessing and fermentation as new eco-polymers and eco-products provides routes to continuous sustainable plastic circularity. These new bioplastics will be fully sustainable and can be readily biologically recycled and regenerated as new bioplastics in a continuous loop akin to biological systems within the natural environment.
Building on the outputs of BioICEP, the EcoplastiC project was formed to develop fermentable waste plastic feedstocks. The project is working to convert these to biopolymers which have built into their performance properties equivalent to petroleum-based plastics, which we are so familiar with today.
€3m EU project on creating sustainable plastic
Launched in October 2022, the EcoPlastiC project is funded by the highly competitive European Innovation Council, which targets high-risk/high-gain visionary innovation. EcoPlastiC technologies are designed to facilitate the full decoupling of polluting plastics consumption from the current extraction of fossil fuels, and instead enable entry into permanent regenerative loops. EcoPlastiC is dedicated to validating novel, highly efficient systems for the depolymerisation of mixed recalcitrant plastics and regeneration as bioplastics through biopolymerisation. These ecoplastics are fully sustainable and can have equivalent properties to virgin petroleum plastics.
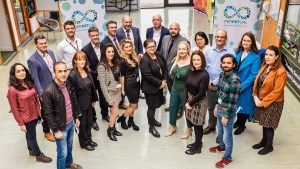
The EcoPlastiC team works closely with consumers, industry and policymakers on an international basis to foster and implement opportunities, creating new prospects for industrial circularity. The new low-carbon plastics will decrease energy consumption, avoid the release of microplastics into the oceans and will help Ireland and the EU meet their sustainability targets.
One exciting development is our new proprietary process for the depolymerisation of waste PET-based plastics.
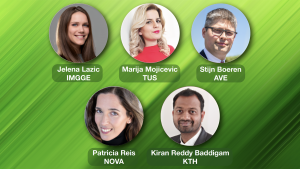
PerPETual: Indefinite recycling for PET sustainable plastic technologies
PerPETual, as the name suggests, is dedicated to the everyday polymer, polyethylene terephthalate (PET), used in drinks bottles, food packaging, and textiles. The €2.9m PerPETual project, funded by Enterprise Ireland’s Disruptive Technologies Innovation Fund, can circularise polyester plastics continuously and positively impact the low-carbon and sustainability targets in the EU’s climate action plans. Co-ordinated by Dr Margaret Brennan Fournet, the science developed in BioICEP has led to the creation of PerPETual innovation. Partnering up with Irish companies, Novelplast and Avoncourt and University College Cork, PerPETual technologies enable continuous recycling for all grades of PET, spanning pristine bottle grades to low-grade PET-based pots, tubs, and trays. Indefinite monomer generation and repolymerisation as ‘new’ virgin PET, equivalent to fossil fuel extracted material, is delivered in this new industrially scalable process.
The PerPETual technology loop starts with washed and pelletised post-consumer waste materials, such as pots, tubs, and trays. By using the PerPETual proprietary green reactive extrusion technology, the material is depolymerised to terephthalic acid, which is purified, ready again for repolymerisation as virgin PET resin.
Legally binding EU directives state that all plastic packaging shall be recyclable in a cost-effective manner or be reusable by 2030 and aims at making recycling profitable for businesses.1 This legislation change in the EU and elsewhere is forcing packaging manufacturers to include a minimum of 25% recycled content in PET packaging from 2025. It also fixes a new target of 55% recycling of polluting plastics waste by 2030, sets a ban on landfilling separately collected waste and fixes stronger arrangements for extended producer responsibility (EPR) schemes. To achieve this, recycling rates will need to improve drastically and will need to include the recycling of lower grade and difficult to recycle PET materials, such as food trays (mono and multilayer), textiles, fibres and bioriented PET films (BOPET).
PerPETual will make a significant contribution towards fulfilling the requirements of binding EU directives by halting resource depletion, landfilling and incineration of polluting plastics, instead converting them into valuable resources and demonstrating the implementation of a circular plastics model.
The technologies applied in BioICEP, EcoPlastiC and PerPETual, spearheaded by the Centre for Polymer Sustainability, demonstrate a seamless sustainable route to a circular economy for plastics by developing an advanced energy-, carbon-, and cost-efficient waste plastic transformation into high market demand bioproducts and bioplastic.
Our keystone BioICEP project invokes the regenerative principles of nature, where materials are continuously repurposed, overcoming issues of the inferior purity and grade quality of the recyclate streams. In the environment, sequential decay and degradation of materials post use occurs, involving processes including mechanical weathering and microbial and enzymatic deconstruction. The output building blocks are then metabolised or biosynthetised and reincorporated as new functional sustainable plastics. This ethos is a template for plastic’s circularity. A suite of scientific and engineering approaches, which operate in tandem with nature’s prescription for regeneration, is being developed to deconstruct and revalorise recalcitrant waste plastic building-block molecules as new eco-friendly equivalent plastics to complete the life cycle for plastics.
These technologies are primed to complete the life cycle for plastics for virtually any plastic materials, including multilayer packaging and flexible films that cannot be cost-effectively recycled to date. The concerted operation of governmental action, scientific progress, business community buy-in and global citizen engagement can provide the power to drive the wheel of circularity and surmount our environmental challenges.
References
- European Commission, “A circular economy for plastics,” can be found under https://publications.europa.eu/en/publicationdetail/-/publication/33251cf9-3b0b-11e9-8d04-01aa75ed71a1/language-en, 2019
Please note, this article will also appear in the fifteenth edition of our quarterly publication.