The Technological University of Shannon is undertaking initiatives to develop low-carbon, industrial-grade plastic packaging solutions that operate within circular lifecycles to address the increasing issue of plastic waste.
In response to the global challenge posed by mounting plastic waste, Technological University of the Shannon (TUS) is leading cutting-edge research to develop food-safe and industrial-grade sustainable polymer alternatives. Led by Vice President of Research, Development and Innovation Dr Liam Brown, TUS’s seven research institutes are working collaboratively to leverage scientific expertise, strategic partnerships and a commitment to environmental responsibility to drive change.
With the newly amended European Packaging & Packaging Waste Directive mandating that a minimum of 55% of all plastic packaging be sustainable by 2030, TUS has intensified its efforts to provide companies with alternatives under the leadership of Dr Margaret Brennan-Fournet, a renowned materials scientist based at TUS’s LIFE Health and Wellbeing Biosciences Research Institute in Athlone.
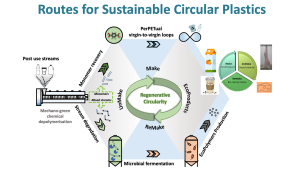
Dr Brennan-Fournet and her team are spearheading initiatives to innovate low-carbon industrial-grade plastic packaging solutions through the cross-institute Centre for Polymer Sustainability. These innovations operate within circular ‘make, unmake and remake’ lifecycles, ensuring sustainability and regenerative processes akin to natural ecosystems. By pursuing a high-risk, high-gain visionary strategy to cultivate the ‘make-unmake-remake’ strategy, the process has the potential for full commercialisation applications ready for industry-grade production.
Make: Indefinitely recyclable, sustainable plastic products manufacturing
Key among TUS’s initiatives is the EcoPlastiC project, funded under the highly competitive European Innovation Council. Working closely with consumers, industry, international partners and policymakers, TUS’s EcoPlastiC project has developed technologies to facilitate the full decoupling of polluting plastics consumption from the current extraction of fossil fuels and instead enable entry into permanent regenerative loops. Applying advanced waste stream fermentation and processing, biodegradable circular plastics and plastic solutions with high performance for the sustainable food packaging sector are being developed as direct alternatives to current polluting petroleum-based plastics.
Examples include:
- High O2 barrier packaging layered composites with equivalent performance to petro-based EvOH.
- Bioadhesives for paper and plastic packaging sealants with equivalent performance to conventional synthetic adhesives.
TUS’s EcoPlastiC prototypes are designed to operate within fully circular life cycles and can be readily ‘unmade’ using new in-house depolymerisation technology, followed by ‘remaking’ within continuous loops. These and further industry-grade products are now available for development with collaborative enterprise partners.
UnMake: Post-use product depolymerisation and degradation with the generation of feedstock streams
Further bolstering sustainability efforts is TUS’s €2.9m PerPETual project, supported by Enterprise Ireland’s Disruptive Technologies Fund. Post-consumer biopolymer and petro-polyesters can now be ‘unmade’ through a new disruptive proprietary low-cost, high-yield green reactive extrusion depolymerisation (Rex) processing system.
The Rex process delivers circularity for the everyday polymer material Polyethylene Terephthalate (PET) with continuous ‘virgin-to-virgin loop’ recycling processes suitable for all grades of PET, spanning pristine grades used in bottles to low-grade pots, tubs and trays with no loss of polymer performance.
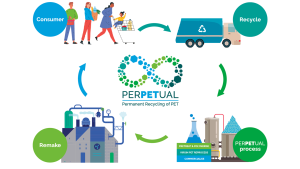
This has the potential to make a significant contribution towards halting finite resource depletion, landfilling, and incineration of waste plastics instead of converting them into valuable resources and demonstrating the implementation of a circular plastics model.
The Rex process can be readily integrated within existing manufacturing lines to depolymerise post-consumer PET waste. Producing Purified Terephthalic Acid (PTA) and Ethylene Glycol (EG), these PET precursor monomers can be readily repolymerized as virgin PET, making it available for use again in food packaging and beyond.
Expansion of the Rex technology makes it effective for mixed PET streams and other petro- and bio-polyesters. This unlocks waste plastic resources, making them available as feedstocks for depolymerisation or fermentation for the manufacturing of regeneratable packaging that operates within cyclical loops. TUS is actively seeking to work with companies requiring circular lifecycles for pure and mixed PET-based streams.
ReMake: Repolymerisation, microbial fermentation and sustainable plastic processing
Regenerative manufacturing not only lowers the ecological footprint of production processes but also seeks to restore and rejuvenate. Within plastic processing, this can be achieved using conventional chemical repolymerisation in the case of pure monomer streams such as PET or via fermentation and biopolymer processing (remake) in the case of mixed feedstocks. The sustainable polymers produced are fully compatible with conventional and state-of-the-art plastic processing and manufacturing techniques, including multilayer film co-extrusion, blown film extrusion, and injection moulding for the fabrication of commercial products for the food packaging sector and broader plastics sectors.
To increase the adoption and uptake of sustainable technologies, TUS is actively engaging with plastic value chain industries, empowering companies to achieve circularity for their products and processes.
Supporting the blue and green environment
A key focus of TUS is to support readily applicable technologies developed to mitigate plastic pollution in waterways, seas and oceans. Working closely with partners in the Atlantic Area and INTERREG PLAST4H2 project, TUS is converting mapped marine litter and plastic waste into valuable products, including hydrogen for energy and eco-friendly plastics.

The opportunities for sustainable packaging developed using TUS disruptive technologies are immense. In 2022, the global food packaging market was valued at $357bn and is expected to reach a market worth of $642bn by 2032. This vast value is starkly contrasted by the fact that a mere 5% of plastic food packaging is currently reported as being recycled within the EU in a closed-loop fashion.
The cutting-edge regenerative technologies at TUS are primed to complete the life cycle of polymers for virtually any plastic material, including multilayer packaging and flexible films that cannot be cost-effectively recycled to date. They aim to determine the most efficient path to commercialisation, with a focus on spin-out formation and future partnerships.
TUS’s Dr Margaret Brennan-Fournet explained: “Our decades-long expertise in polymer research and commitment to circular practices has positioned us uniquely to meet the current and future demands for eco-packaging solutions through the development of sustainable polymer alternatives. Our regenerative technologies are not only eco-friendly but also commercially viable, ready for industry-grade production. We invite companies to collaborate with us in developing these circular and sustainable technologies for polymer and plastic food packaging products to meet their needs, ensuring a positive impact on our environment and economy.”
Please note, this article will also appear in the 19th edition of our quarterly publication.