TotalEnergies introduces its revolutionary water-based lubricant (WBL) that provides a paradigm-shifting advancement for electric vehicle lubrication.
Thermal management of previous generations of electric vehicles (EVs) with high power density requires direct cooling strategies in which the cooling fluid is in direct contact with the hot spots of the electric motor. In a Permanent Magnet Synchronous Motor (PMSM), the stator end winding and rotor magnets generate a certain amount of heat that cannot be properly cooled down by a conventional water jacket cooling. Hence the development of direct oil cooling technology in which the transmission oil is used as a coolant for the electric motor. This new cooling architecture generally implements a hollow rotor shaft where transmission oil flows. In addition, holes located at both edges of the rotor shaft allow the transmission oil to be splashed on the end windings thanks to centrifugal force. The direct oil cooling system significantly improves heat transfer.
This shift was not motivated by the fact that a transmission oil has superior cooling properties than a water-based coolant. On the contrary, water is often an ideal cooling fluid due to its high thermal conductivity (factor of four compared to oil), high heat capacity (factor of two), and low viscosity. However, it was thought that water application is unfeasible for two main reasons. Firstly, the cooling fluid directly interacts with electrical components, where high electric currents and voltages occur. Hence, it is required to have a very low electrical conductivity, which is advantageously reached by lubricating oils. Secondly, the fluid comes in direct contact with gears and bearings, for it should have lubricating qualities, which gives another advantage to lubricating oils compared to water.
All these aspects can be improved through the chemical formulation of water. Our goal was to develop an innovative water-based lubricant which possesses good lubricating properties while maintaining the outstanding cooling property of water. Our WBL can meet all the requirements for a single fluid designed for lubricating and cooling the Electric Drive Unit (EDU). The use of a WBL can even outperform lubricating oils in many characteristics, especially with an environmental footprint, which opens the door to a revolution in the lubricant and car industries.
TotalEnergies’ water-based lubricant enhances cooling efficiency
TotalEnergies developed a simulation workflow to study electric motor cooling. The different simulation tools illustrated in Fig. 1 allow us to approach the electric motor’s thermal modelling comprehensively.
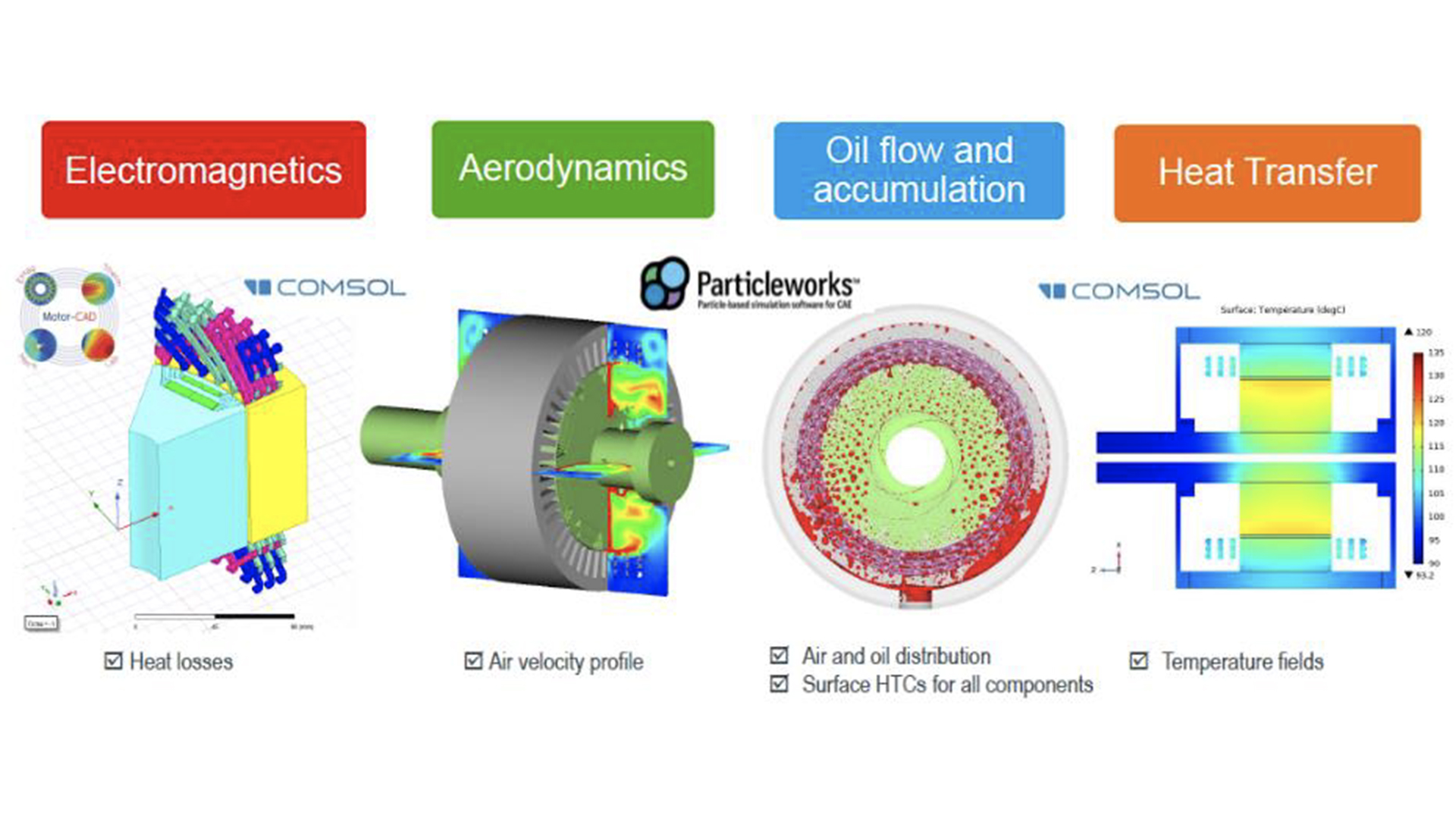
Articulating the workflow, one operating condition typical of an e-motor efficiency map was selected: 6000 rpm with a torque of 90 N.m. It represents a car driving steadily at 70 km/h. Two fluids were compared within the direct liquid cooling architecture: a reference oil-based lubricant and TotalEnergies water-based lubricant. The direct liquid cooling system comprises a hollow shaft and four channels located on the front and rear of the shaft, as shown in Fig. 2. Liquid is splashed on end windings via the four channels thanks to the centrifugal force provided by rotor rotation. The fluid inlet temperature is 60°C, and the flow rate is 5 L/min.
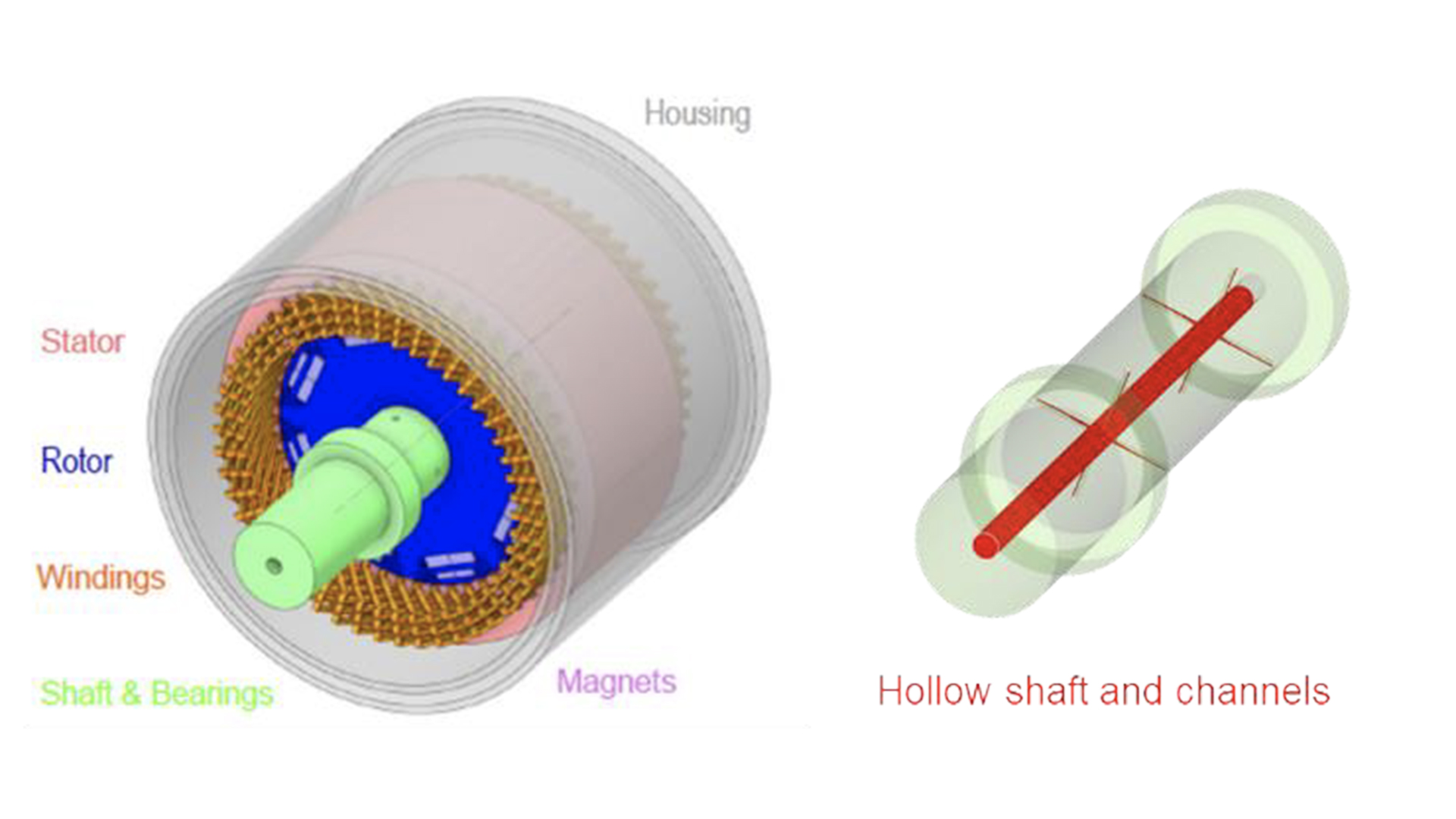
We used Particleworks, a meshless CFD software based on Moving Particle Simulation (MPS). The MPS Method was originally proposed by Professor Koshizuka to provide flexible modelling and simulation for complex moving boundary problems.1 Thanks to its meshless feature, it is particularly adapted to manage complex geometries such as e-motor windings or moving parts such as the rotor.
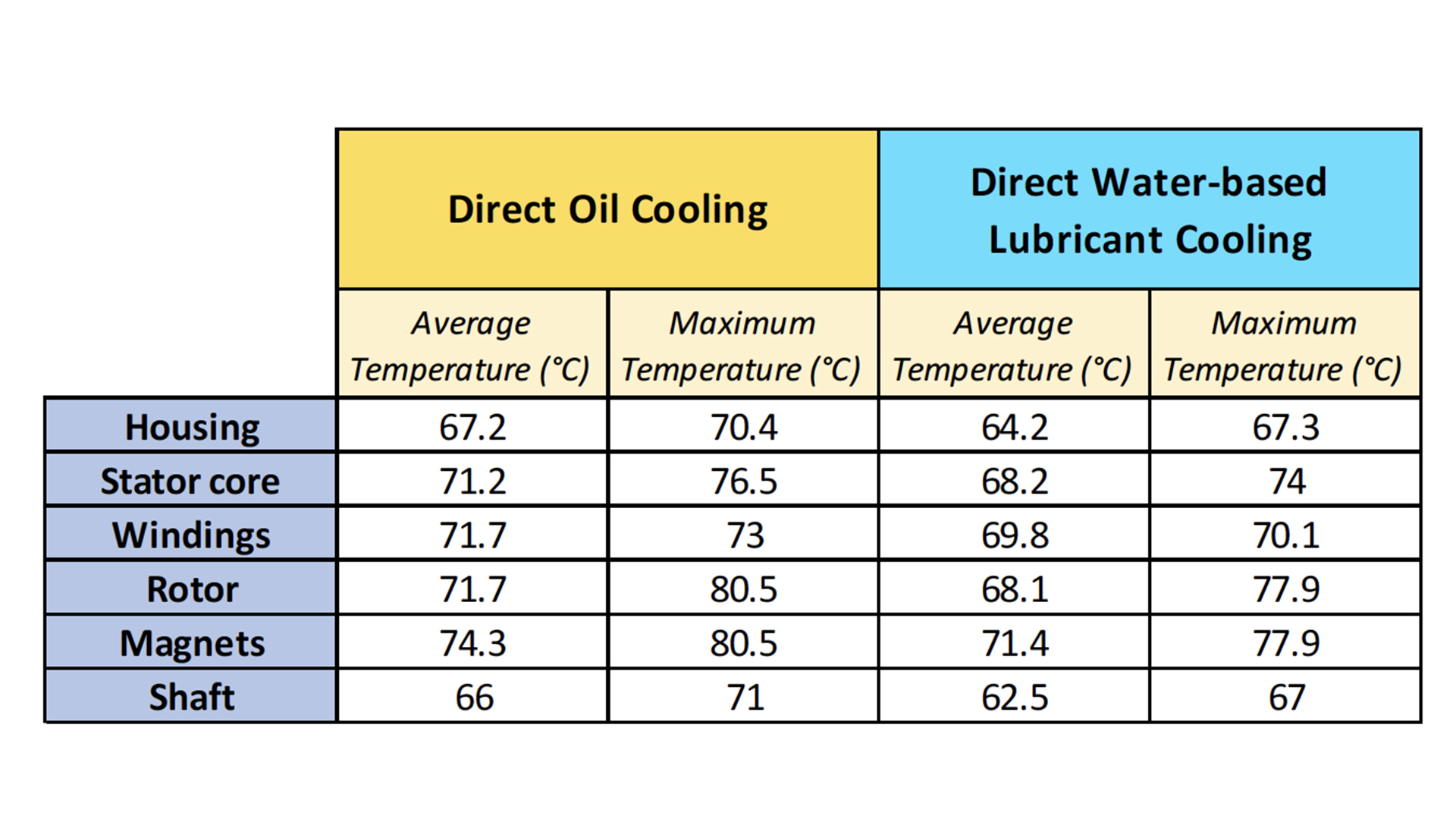
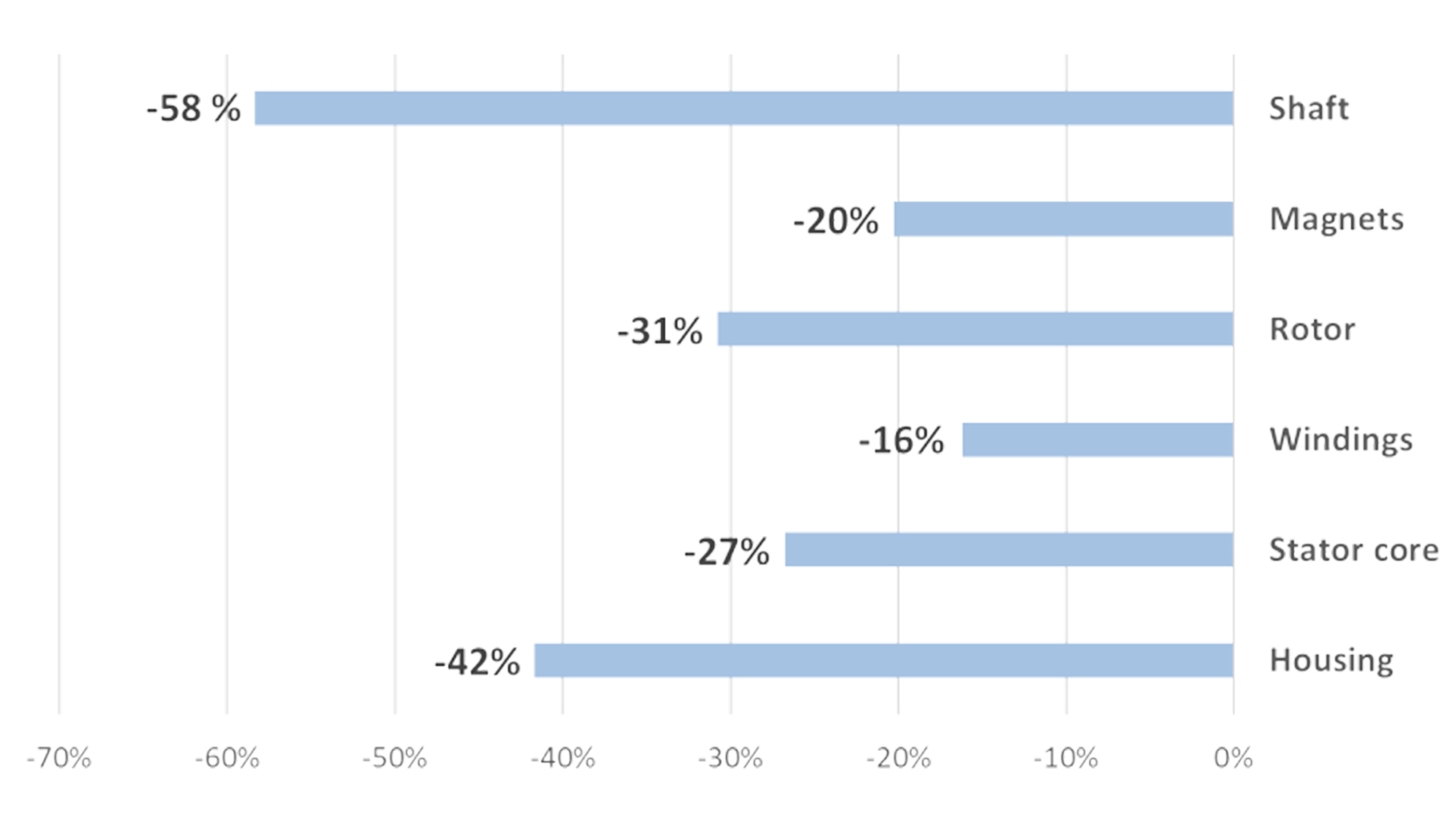
Results shown in Fig. 3 and Fig. 4 confirm that TotalEnergies’ water-based lubricant provides better cooling of the e- motor. From -16% in the windings to -58% in the shaft, a significant temperature reduction has been calculated for each part of the e-motor. Even at a very low viscosity value, those temperature reductions would not have been attained with an oil-based lubricant. Water’s superior heat transfer ability allows TotalEnergies’ WBL to reach this outstanding cooling performance. Direct cooling with a WBL paved the way to a higher power density e-motor and optimised cooling strategy.
Material compatibility
One main factor preventing using a water-based lubricant for direct e-motor cooling is the fear of current leaking due to water’s high electrical conductivity. It is true that direct contact between water and metallic copper would have led to deadly consequences. However, there is never direct contact between the cooling fluid and metallic copper in the e-motor. Copper wires are coated with several layers of insulation materials. Generally, the chemistries of the wire enamels include polyester (PE), polyester-imide (PEI), polyamide-imide (PAI) or polyether-ether-ketone (PEEK). The insulation system can be strengthened even more by adding a layer of impregnation resin. Therefore, one can assume that the electrical insulation property is fully supported by the wire insulation materials, and a water-based cooling fluid can be used if it has good compatibility with insulation materials.
The partial discharge (PD) test is a powerful tool to check the insulation property of winding materials. PD is a localised breakdown phenomenon across a portion of the insulation between two conductors.2 This happens when the electric field strength exceeds the breakdown strength of a portion of the insulating material. PD can lead to the failure of the insulation system. The voltage value needed to initiate PD is the partial discharge inception voltage (PDIV). Once initiated, PD will continue until the voltage falls below the partial discharge extinction voltage (PDEV).
PDIV and PDEV measurements were carried out on Damid 200 (mixed PEI/PAI coating) twisted pairs. Twisted pairs are made up of two insulated copper wires that are twisted together. The twisted pairs are immersed in our water-based lubricant for different ageing times in an oven at 90°C and compared to a reference group of twisted pairs that were not immersed in any fluid, as shown in Fig. 5.
Then, PDIV and PDEV are measured at different ageing times with a High-Voltage generator. In Fig. 6, the results of the experiments are shown.
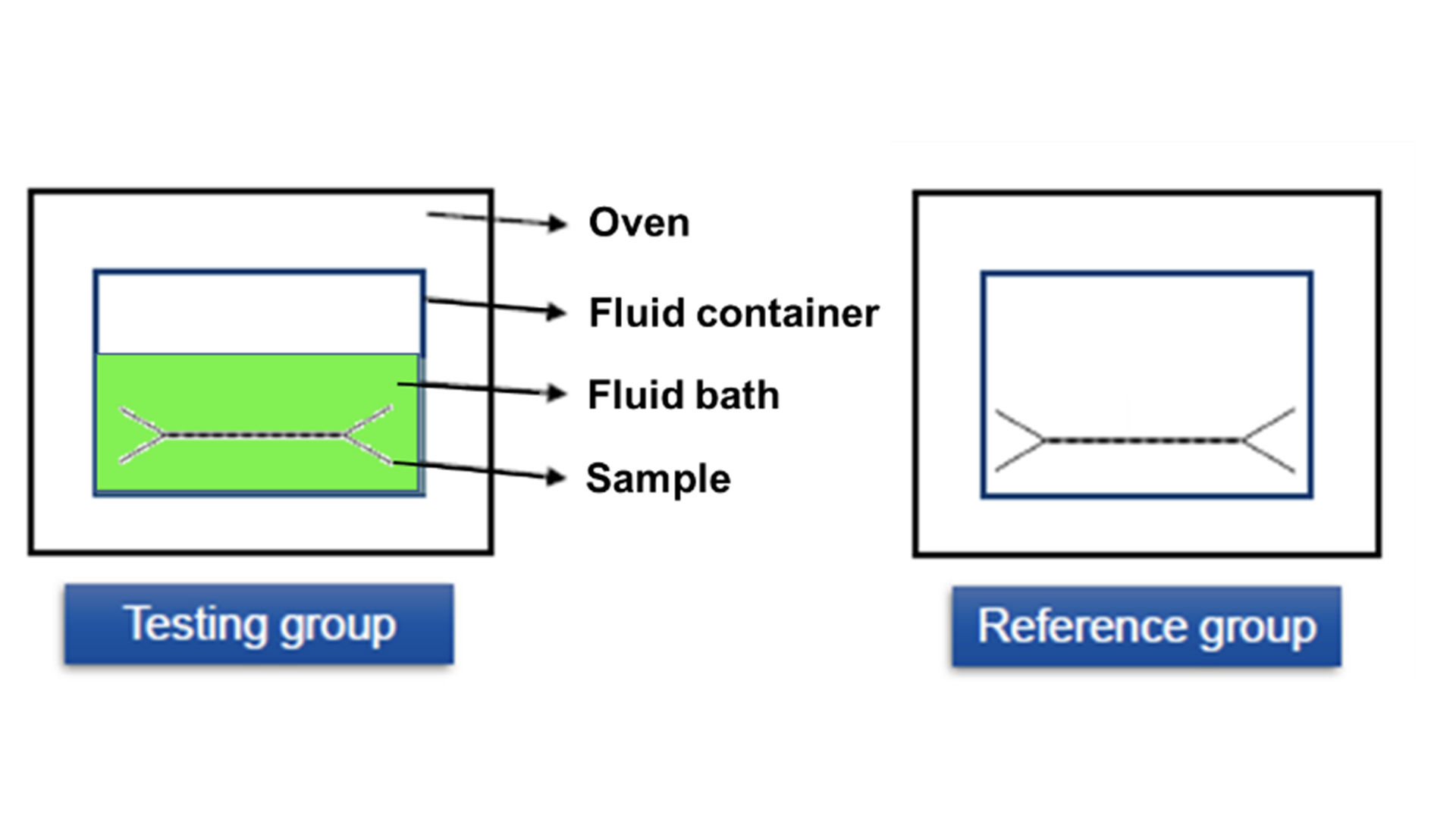
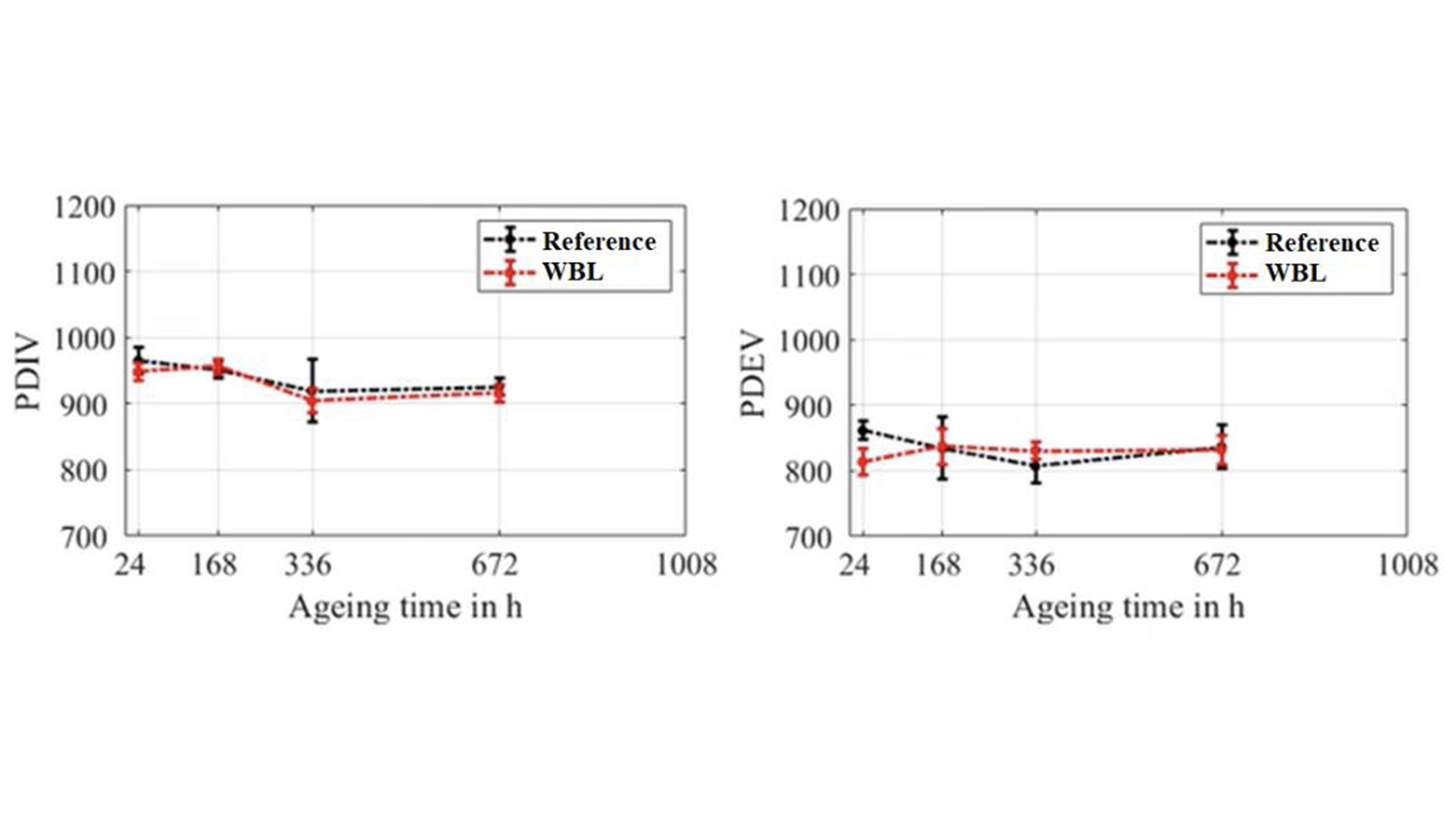
From 24 to 672 hours, the overall PDIV and PDEV remain at a relatively stable value and close to the reference, which clearly indicates that TotalEnergies’ WBL is compatible with winding wires. Even after an ageing process of 672 hours in TotalEnergies’ WBL, the winding wire is keeping its pristine electrical insulation property.
Water-based lubricant superlubricity in EHL
Water-containing fluids display exceptional friction behaviour. They are capable of achieving what is called superlubricity, that is to say, the state of ultra-low friction between two surfaces in relative motion. A friction coefficient at the order of 0.001 was measured in EHL conditions in many studies.3 They explain that superlubricity is achieved because of the formation of a hydration layer that easily accommodates shear, which results in ultra-low friction.4
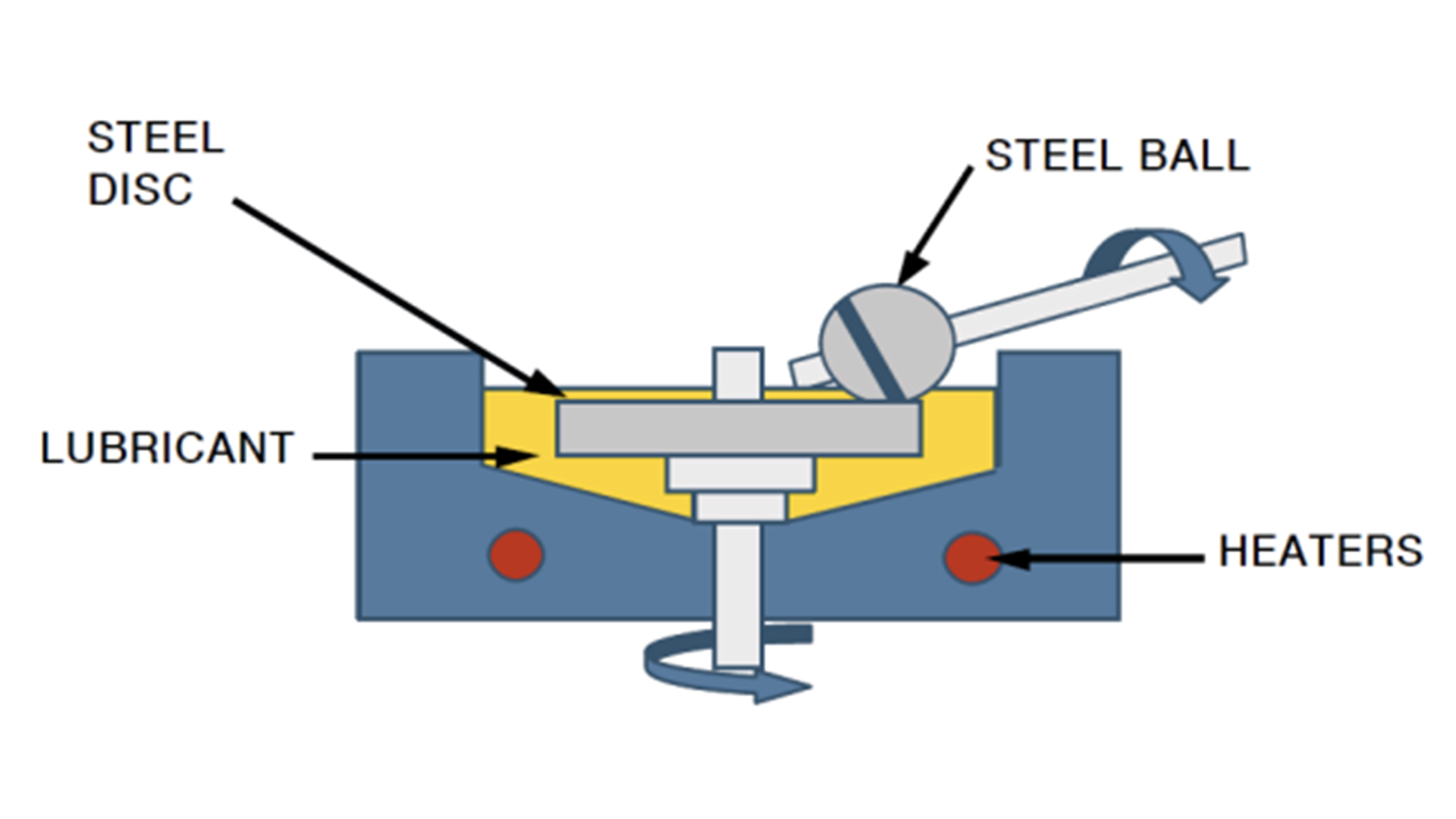
Friction measurements were performed using the ball-on-disc technique implemented by the Mini-Traction Machine (MTM) designed by PCS Instruments. Fig. 7 shows a schematic view of the tribometer. The steel ball and disc are immersed in lubricant. They are driven by separate motors at a given rolling/sliding condition, and the friction coefficient is measured during the test. Experimental settings representative of the EHL regime were applied: a maximum Hertzian pressure of 1.2 GPa, an entrainment speed of 1 m/s, a test temperature of 40°C, and various slide-to-roll ratios (SRR) to draw a full friction curve. Two fluids were experimented with, our TotalEnergies water-based lubricant and a reference EV fluid, an oil-based lubricant.
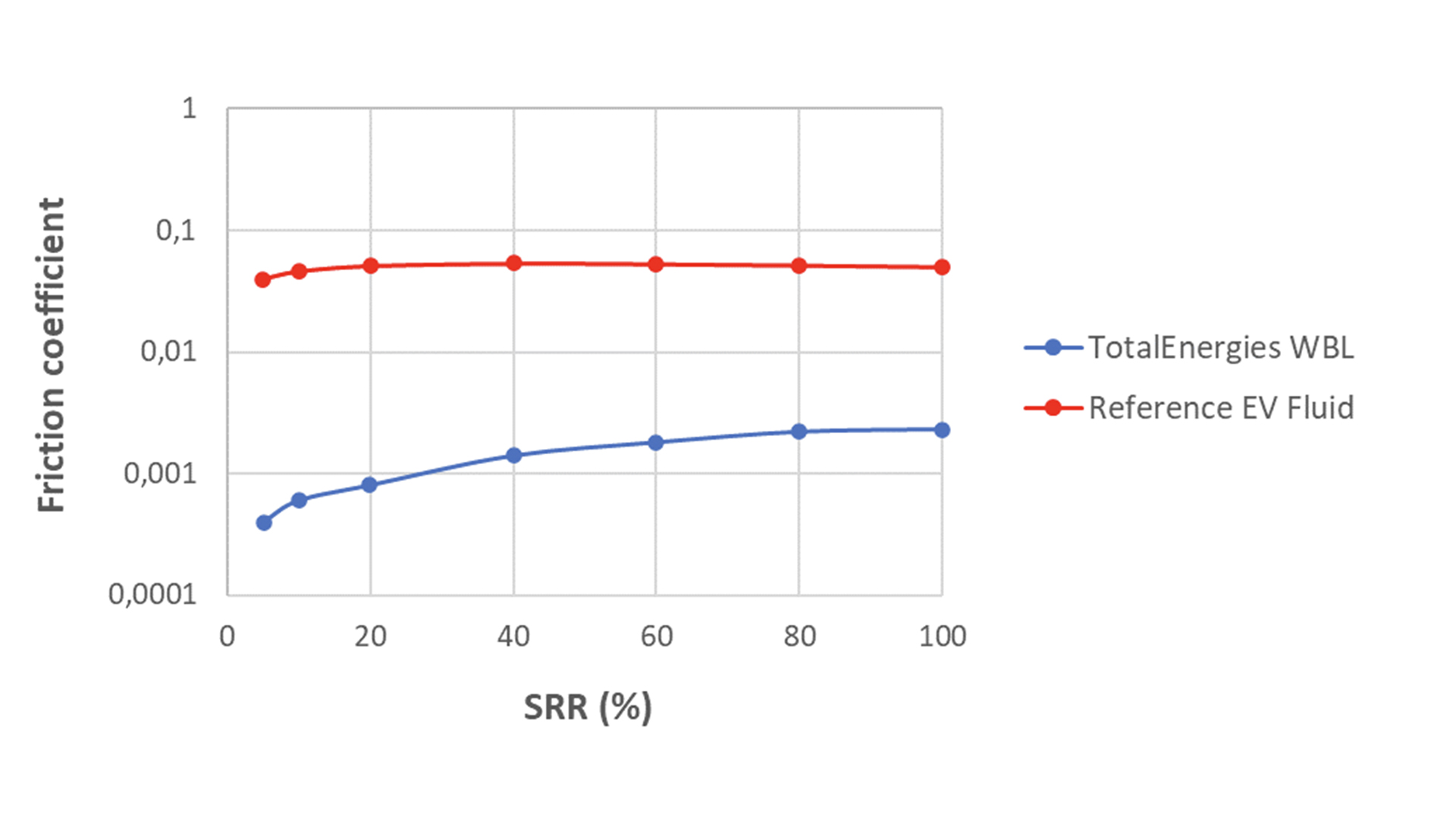
Results in Fig. 8 clearly show the superlubricity phenomenon achieved by TotalEnergies’ WBL. The friction coefficient varies from 0.0004 to 0.002 by increasing the SRR from 5% (nearly pure rolling) to 100% (pure sliding), while the reference EV fluid has almost two higher orders of magnitude. There is a qualitative gap between the friction behaviour of WBLs and oil-based lubricants.
Managing boundary lubrication regime
Water is not a piezoviscous liquid; its pressure sensitivity is much less pronounced than oil.5 The oil viscosity increases dramatically with pressure, approximately doubling for every 50 MPa increase, thus helping to build up a thicker lubricating film thickness in contact operating at high pressure. The poor pressure-viscosity response of water makes the water-based lubricant film thickness roughly 50% lower than for oils, and the transition from safer full film lubrication to the riskier boundary lubrication regime more likely.6
Scuffing performance
One of the gear failure modes related to the boundary lubrication regime is gear scuffing. Scuffing occurs in contact operating at high pressure and high sliding speed when the lubricating film in the contact collapses, resulting in extensive wear damage.7 Various studies ascribed the anti-scuffing performance to the growth of a protective tribofilm on the surface. The tribofilm results from a chemical reaction between lubricant antiwear/extreme pressure additives and contact asperities under tribological stresses. Under the context of water-based lubrication, the additives must be carefully chosen to withstand boundary lubrication constraints.
The standard FZG tests A20/8.3/90, A10/16.6/90, and S-A10/16.6R/90 are widely used for the evaluation of scuffing properties of gear oils. The FZG Scuffing Tests consist in increasing stepwise the load applied to the sump-lubricated gear pair run at a constant speed. After each load stage, the tooth flanks are inspected for surface damage and any changes in appearance are noted. The failure load stage (FLS) is reached if the summed total width of damage present on all teeth of the pinion gear is estimated to be equal to or exceeds the width of one tooth. The test is considered complete when either the failure criterion has been met or when load stage 12 is run without meeting the failure criterion.
The A10/16.6/90 version is more severe than A20/8.3/90 as the pitch line velocity is increased from 8.3 to 16.6 m/s, and a narrower pinion with a 10 mm width instead of 20 mm is used, which increases the contact pressure. The shock test S- A10/16.6R/90 is the most severe FZG test, as the load is not applied gradually. There is no running-in, so the contact surfaces are not smoothened, which leads to higher mechanical constraints. It should be mentioned that the temperature of the standard procedures was lowered to 60°C to be adapted to the ‘WBL study’. For a given thermal stress, the water temperature would be lower than the oil, thanks to its better cooling capacity.

Results are presented in Fig. 9. Generally, most EV fluid specifications require an FLS higher than 12 in FZG A20/8.3/90. TotalEnergies’ water-based lubricant meets that requirement and can withstand more severe versions of FZG with a very good performance.
Pitting performance
Micropitting is a type of surface fatigue that is very common in gears and roller bearings. ISO 15243 defines this damage as surface-initiated fatigue.8 Ueda et al. stipulate that it is caused by stress fluctuations due to roughness asperity interactions in rolling-sliding contacts.9 It manifests itself by forming burnished areas, asperity microcracks and asperity microspalls.
The MPR (Micro Pitting Rig) designed by PCS Instruments is widely used to assess micropitting performance. The MPR is a three-contact disc tribometer in which three rings with a diameter of 54mm are simultaneously in contact with a central roller with a diameter of 12mm. This geometric arrangement displayed in Fig. 10 allows the test roller to be subjected to many contact cycles over a short period, promoting micropitting. The test is carried out for a period of 20 hours. The micropitting phenomenon is detected by an accelerometer connected to a vibration monitor. The monitoring of the vibration signal can be used to determine if micropitting has occurred within the material. An optical micrograph of the rubbing track along the rolling direction will confirm the generated damage is indeed micropitting.

The test procedure implemented in this study was specifically developed to evaluate the micropitting performance of gear lubricants concerning their performance in the FZG C/9/90 test standard. Only the test temperature was changed to 60°C to be adapted to WBLs. Two fluids were experimented with, our TotalEnergies WBL and a reference electric vehicle (EV) fluid. Results are shown in Fig. 11.
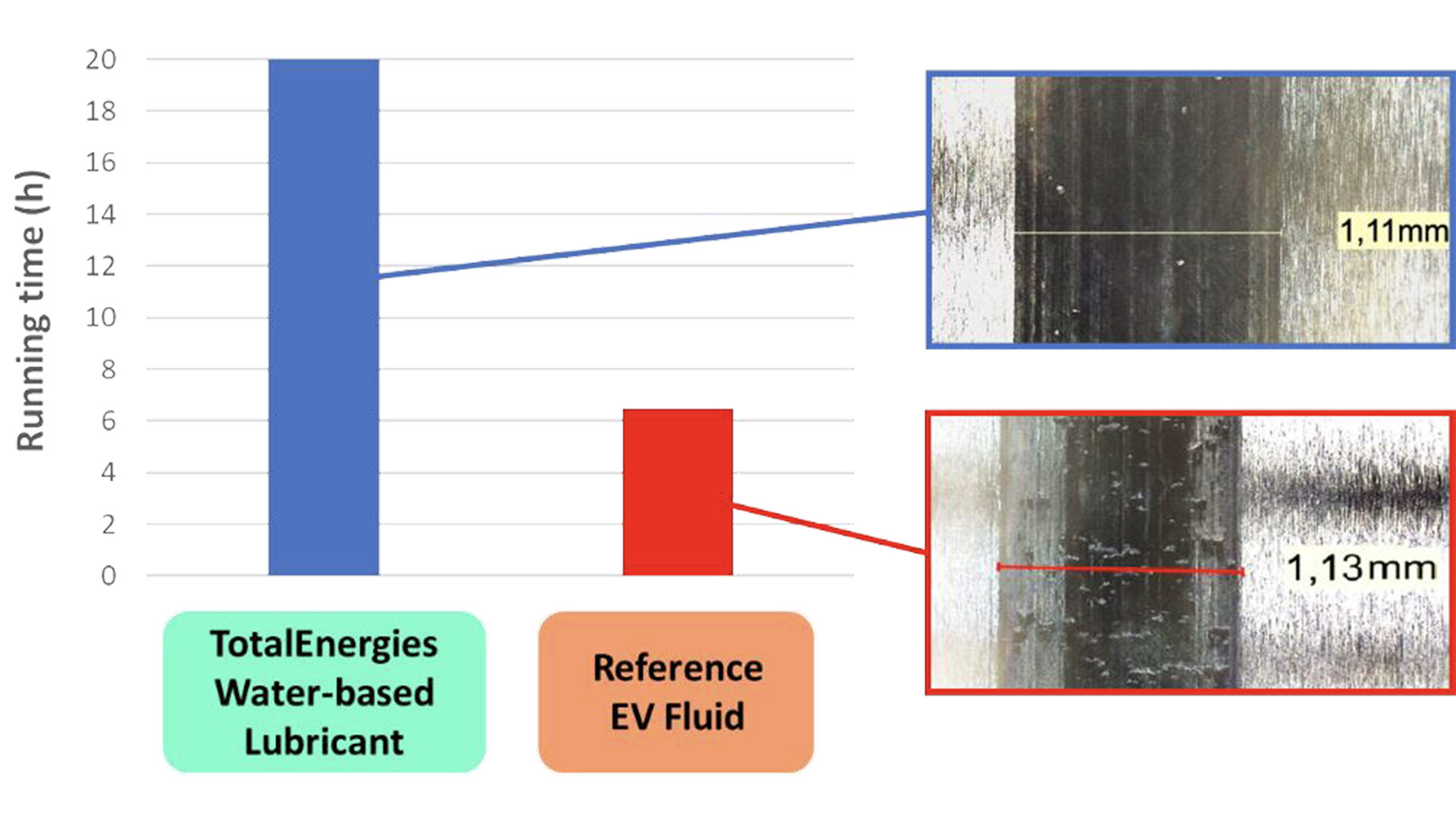
The micropitting performance is described as poor if the micropitting time is less than ten hours, average if the micropitting time is between ten and 15 hours, and good in the absence of micropitting after more than 15 hours of testing. It can be seen that TotalEnergies’ water-based lubricant is capable of fulfilling the whole test duration without manifesting any surface cracks typical of micropitting. It is not the case for the reference EV fluid, which fails at 6.5 hours and shows a significant number of surface cracks across the rubbing track, with a ‘V’ shape, typical of surface-initiated fatigue. It is a clear sign of a micropitting process taking place.
Life Cycle Assessment
Given the importance of tackling climate change and the environmental considerations in today’s world, it is essential that the lubricant industry includes the sustainability aspect in the assessment of its products. Thus, eco-design is essential to reduce the environmental footprint of a lubricant over its whole life cycle. One of the expected added values from the design of a WBL is its lower environmental impact.
Regarding this aspect, a Life Cycle Assessment (LCA) was performed according to Product Environmental Footprint (PEF) multicriteria methodology using the Ecoinvent 3.8 database to compare TotalEnergies’ WBL with its oil-based conventional counterpart.
The issue when dealing with LCA is the lack of reliable data, especially when many processes are involved. That is why a ‘cradle-to-gate’ analysis was conducted, considering raw material extraction, transportation of raw materials, and the blending process at TotalEnergies’ plants, for which the data are well-known (system boundaries calculation). The focus was on the three following environmental indicators which are relevant regarding the activity of the company and the field of application of the lubricant:
- Global warming potential, defined by the carbon dioxide equivalent (kgCO2eq), according to IPCC 2013;
- Water use (m3), according to the AWARE100 methodology; and
- Resource use, fossils (MJ), according to CML v4.8.
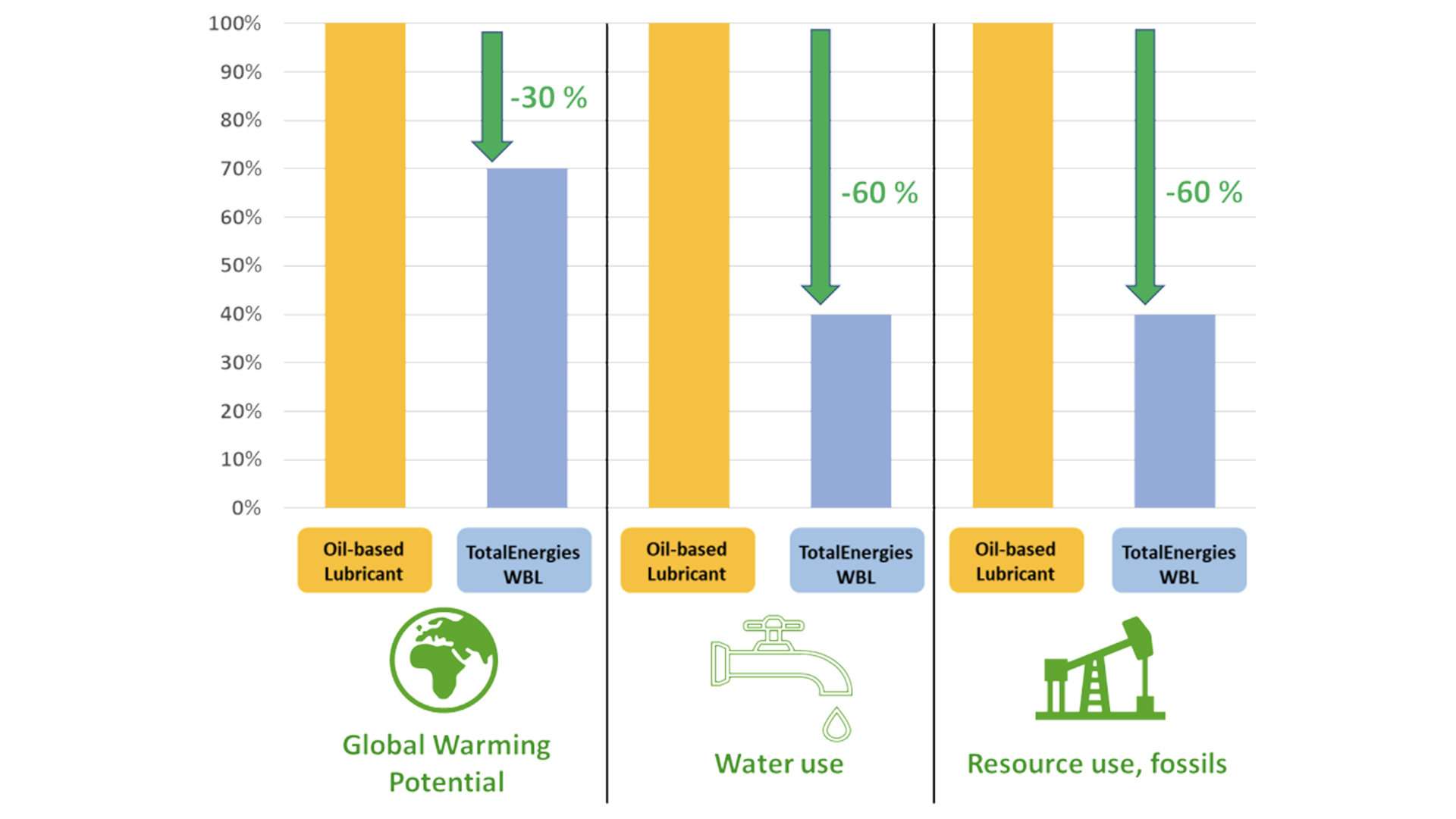
Results of the LCA displayed in Fig. 12 indicate the environmental benefits of TotalEnergies’ WBL. A reduction of 30% in global warming potential and a reduction of 60% for both water and resource use. The environmental benefits of considering WBL have been demonstrated on these three main environmental indicators thanks to LCA.
Thanks to intensive research from TotalEnergies R&D Team and partners, TotalEnergies’ WBL promises to advance the EV lubricant landscape, and the company is still striving to formulate stepped-out fluid technology for the future challenges of e-mobility.
Acknowledgements
TotalEnergies would like to express our gratitude to B. Eng Yu Cao and M. Sc. Liguo Yang from IEM RWTH Aachen University for their valuable work on compatibility tests on insulation materials. We would like to express our thanks to our colleagues Goulven Bouvier, Maria Rappo, Julien Chaminand, Shimin Zhang, Eric Tinguy, Mathieu Desormeaux, Francis-Olivier Ramoni for the R&D work on e-mobility.
References
- Koshizuka S.: ‘Moving particle semi-implicit method for fragmentation of incompressible fluid’, Nuclear Science and Engineering, 1996.
- Seifi S., Werle P., Shayegani Akmal A. A., Mohseni H., Borsi H.: “A feasibility study on estimating induced charge of partial discharges in transformer windings adjacent to its origin”, International Journal of Electrical Power & Energy Systems, July 2021.
- Chen, Z. Liu, Y.; Zhang, S.; Luo, J.: Controllable Superlubricity of Glycerol Solution via Environment Humidity. Langmuir 2013, 29, 11924–11930
- Baykara M. Z., Vazirisereshk M. R., Martini A.: “Emerging superlubricity: A review of the state of the art and perspectives on future research”, Applied Physics Reviews 5, 041102 (2018).
- Bair S.: “High-Pressure Rheology for Quantitative Elastohydrodynamics, Second Edition, Elsevier, 2019
- Larsson R., Rohfleisch S., Zapata Tamayo J. G., Vrcek A., Björling M., Shi Y.: “Micropitting performance of a Water- based Lubricant”, 7th World Tribology Congress, WTC 2022, July 10-15, 2022, Lyon, France.
- Bayat R., Lethtovaara A.: “Scuffing evaluation of fully formulated environmentally acceptable lubricant using barrel-on- disc technique “, Tribology International, vol. 160 (2021), art. 107002.
- ISO Standard 15243: Rolling Bearings—Damage and Failures—Terms, Characteristics and Causes (2004).
- Ueda M., Spikes H., Kadiric A.: “In-situ observations of the effect of the ZDDP tribofilm growth on micropitting”, Tribology International, vol. 138 (2019), pp. 342-352.
Please note, this article will also appear in the thirteenth edition of our quarterly publication.