Aluminium is a crucial component of the green transition. Speira addresses the issue of sustainability in the aluminium industry, developing innovative solutions to ensure a stable supply of green batteries.
Battery electric vehicles (BEVs) are seen as the cornerstone of a more sustainable future of transport. Batteries are the key technology for powering these vehicles. However, the production of battery cells involves energy-intensive processes that result in significant CO2e emissions.
As a result, BEVs have a higher carbon footprint in production than internal combustion engine (ICE) vehicles. McKinsey’s projections and industry targets indicate that CO2e emissions from battery production can be significantly reduced. This study examines how aluminium components, such as the cell housing and the battery electrode foil, impact emissions today and what steps need to be taken to achieve meaningful carbon footprint reductions in future battery products.
Decoupling growth from carbon emissions in road transportation powered by BEVs
Batteries are a key technology for achieving the Paris Agreement’s 1.5°C target and net-zero emissions by 2050. This will be achieved primarily by enabling the decarbonisation of transportation and supporting the generation and distribution of renewable energy. According to the International Energy Agency (IEA), in 2022, transportation accounted for around 8 Gt and a share of 23% of the global greenhouse gas emissions, see Fig. 1. Decarbonising the transport sector is therefore critical to achieving the 1.5°C target and carbon neutrality by 2050.
The electrification of transport and mobility is driven by the need to decarbonise logistics and individual traffic. The advantage of BEVs is that they have a very low carbon footprint during operation.
However, battery cell production is currently an energy- and greenhouse gas emission-intensive process, with the battery accounting for around 60% of the embedded greenhouse gas emissions from BEV production. Hence, there is a need to decarbonise battery cell production, which is recognised by legislators, automotive OEMs, and the battery industry.
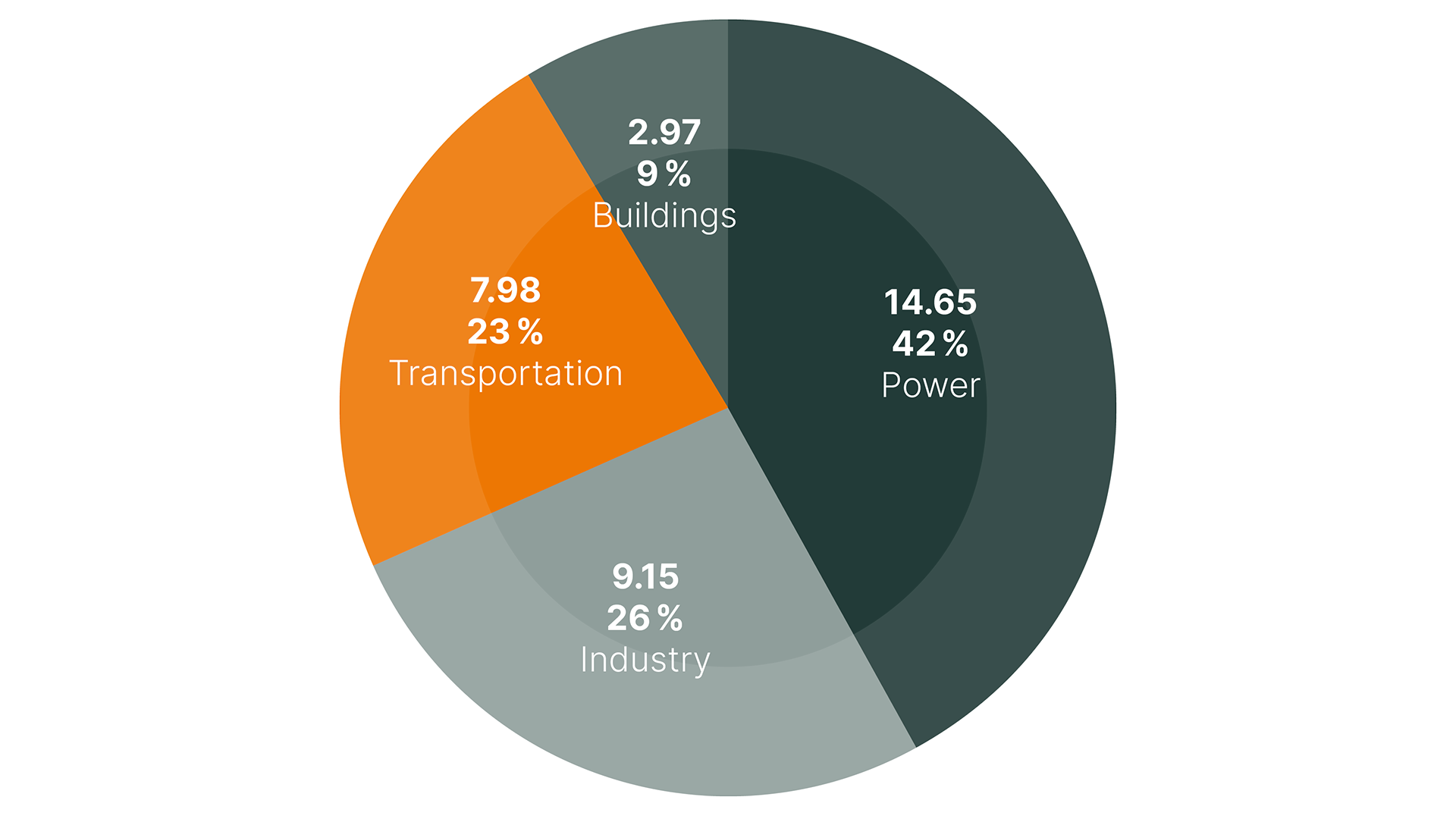
Addressing each step of the supply chain
To achieve meaningful reductions in emissions during the production of batteries, every step of the value chain will have to contribute significantly to reducing greenhouse gas emissions. The greenhouse gas emissions from battery cell production originate from mining and refining, active material production, components and logistics, and cell manufacturing. In total, 97kg of CO2e are emitted during the production of 1 kWh of battery energy today, see Fig. 2.
McKinsey projects that the total greenhouse gas emissions from battery cell production could be reduced to 12 to 24kg of CO2e per kWh by 2030. Some battery cell producers like Northvolt have set themselves an even more ambitious goal of 10kg of CO2e per kWh by 2030.
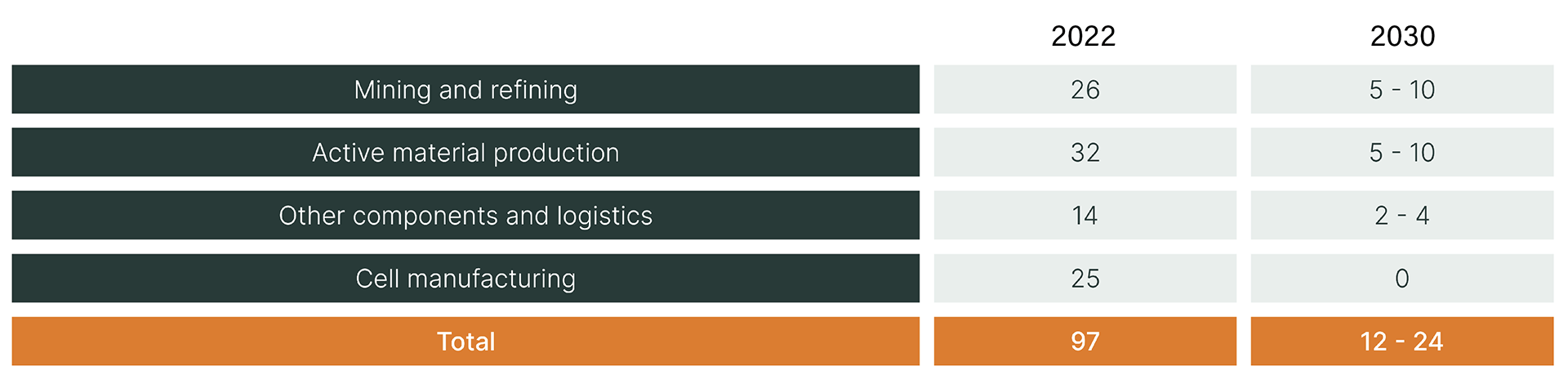
In order to come close to the projected target, greenhouse gas emissions will have to be reduced in all the segments mentioned. It should be noted that 7-14kg of CO2e per kWh can be attributed to the extraction and refining of raw materials and the production of other components. These segments include the production of aluminium-based components such as battery cell housings and electrode foil. In the following section, we take a closer look at the production of aluminium and its impact on the carbon footprint.
The importance of aluminium
On average, the battery cells of a current BEV contain more than 30kg of aluminium – in respect to a battery pack with 60kWh of LIB energy storage (considering only the electrode foil and cell housing).
Aluminium’s unique properties make it the go-to material for battery applications. With the high conductivity of aluminium, the battery’s internal and external electrical resistance can be kept low, allowing high charging speeds. Paired with the low specific weight of aluminium, it is not by chance that aluminium plays a vital role in state-of-the-art lithium-ion batteries.
Batteries are the central component of a BEV’s powertrain. Therefore, batteries need to cater to the specific needs of each vehicle, either by offering high-cost effectiveness in production and sturdiness, such as LFP-based batteries, or by offering higher energy densities, such as NMC and NCA chemistries. Thus, a multitude of different cell chemistries are used today to power modern BEVs. Aluminium plays a significant role in each of them, as it is used for the electrode foil, as the cell casing, or for different kinds of connectors. Depending on the cell chemistry, 0.5-0.7kg of Al aluminium is required for the production of 1kWh of lithium-ion battery energy storage. As shown in Fig. 3, this is equivalent to a minimum of 30kg of aluminium per BEV.
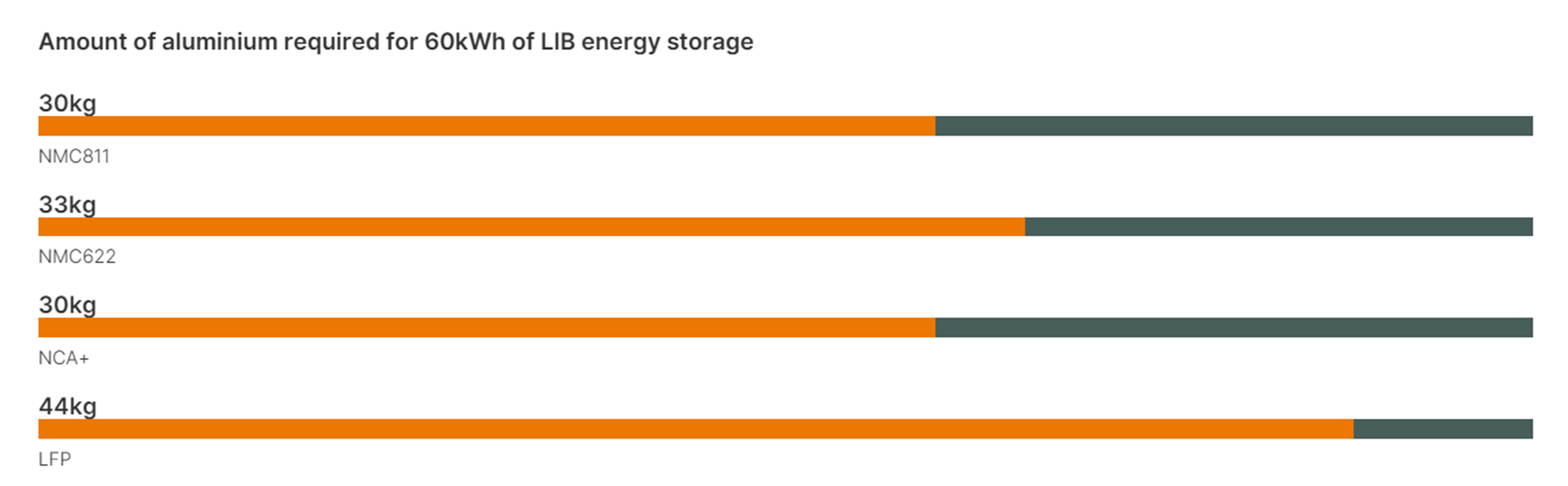
Reducing aluminium’s carbon footprint
In the production of aluminium, the energy source and the amount of recycled material determine the carbon footprint.
Considering the world average, the production of 1kg of primary aluminium requires about 14kWh. Industry leaders might achieve a level of 12.3kWh. Here, the energy mix employed to produce primary aluminium is decisive for greenhouse gas emissions. On the other hand, recycling aluminium requires up to 95% less energy than the production of primary aluminium, where the use of external production scrap and end-of-life scrap allows for a significant reduction in greenhouse gas emissions. It is, therefore, crucial to have transparency regarding the greenhouse gas emissions from aluminium in kilogramme of CO2e per kilogramme of Al considering the semi-finished product, see Fig. 4.
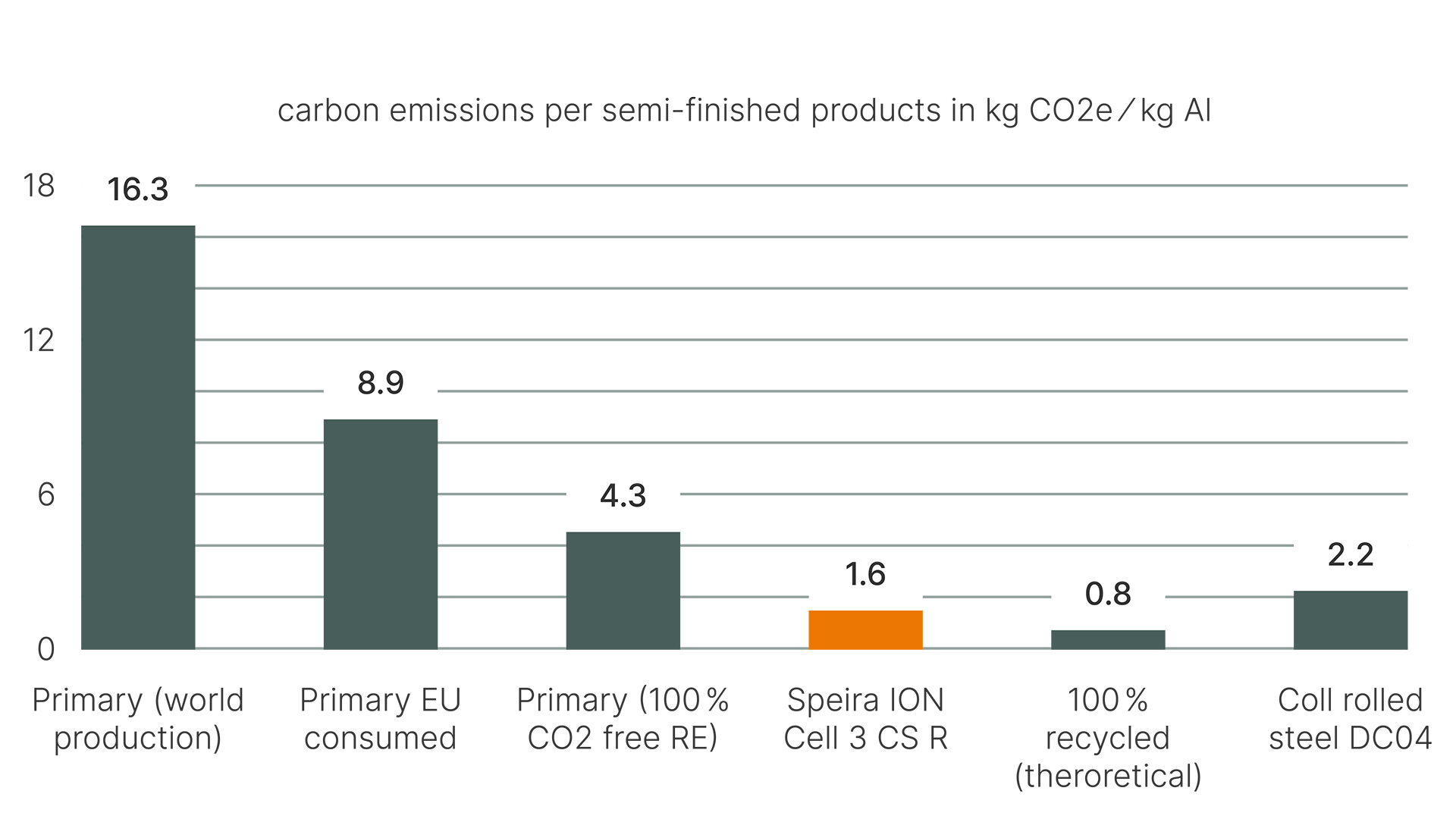
For simplification reasons, the carbon footprint effects of semi-production processes, such as rolling, cutting, and annealing, are considered within this study by a constant factor of 0.3kg of CO2e per kilogramme of Al, which is a typical value for aluminium semi-production. Considering mine-to-slab primary production, the use of 100% carbon footprint-free renewable energies (RE) during electrolysis allows for a 75% reduction of greenhouse gas emissions compared to the world average. The use of aluminium alloys, which allow the possibility of accepting an increase in recycled content, enables a further significant reduction in greenhouse gas emissions.
Drawbacks in battery cell housing applications
While it is the obvious choice in terms of carbon footprint, not all applications allow the use of recycling-based alloys.
The requirements of a component are decisive for the applicability of alloys based on primary or recycled aluminium. For instance, applications with the highest conductivity requirements, such as connectors, can only be satisfied with commercial pure aluminium (1xxx). Hence, these products will typically be primarily aluminium-based. Regarding the battery cell, the same is to be expected for electrode foil and cell-to-cell connectors.
Currently, battery cell housings are made of the aluminium alloy AA3003. While this material is established and fulfils all the technical requirements of a deep-drawn cell housing, it has one distinct disadvantage. Its restricted chemical composition requires a high content of primary material. Consequently, the use of recycled content will be limited, and greenhouse gas emission reductions below 4.0kg of CO2e per kg of Al will be hard to achieve.
Alternative material concepts like Speira ION Cell 3-CS R or Speira ION Cell 3-PS R enable a significantly increased share of recycled content in conjunction with very low greenhouse gas emissions while fulfilling all the requirements of a battery cell housing material such as formability, strength, electrolyte compatibility, and weldability.
Creating a more sustainable aluminium industry
If we stick to the currently established material solutions, aluminium itself could be responsible for as much as 20% of all emissions, even if it were produced with 100% renewable energies.
Based on the foregoing evaluation, aluminium’s contribution to total greenhouse gas emissions from lithium-ion battery cell production can be assessed. The previously shared data enables a top-down assessment without considering the applicability of individual material solutions to aluminium-based battery components.
The impact of the aluminium components’ carbon footprint will be minor in 2022, regardless of the aluminium source. However, this picture will change significantly if battery cell production emissions decrease as projected. Assuming the lowest projected greenhouse gas emissions from lithium-ion battery cell production of 12kg of CO2e per kWh could be realised (McKinsey scenario ‘Low’), the application of primary aluminium featuring world-average greenhouse gas emissions would result in a disproportionately high contribution to greenhouse gas emissions.
In this scenario, the greenhouse gas emissions from aluminium account for 75% of the total greenhouse gas emissions from the projected battery cell production. The application of primary aluminium, which is currently consumed in the EU as of today, would account for 41% of the total greenhouse gas emissions.
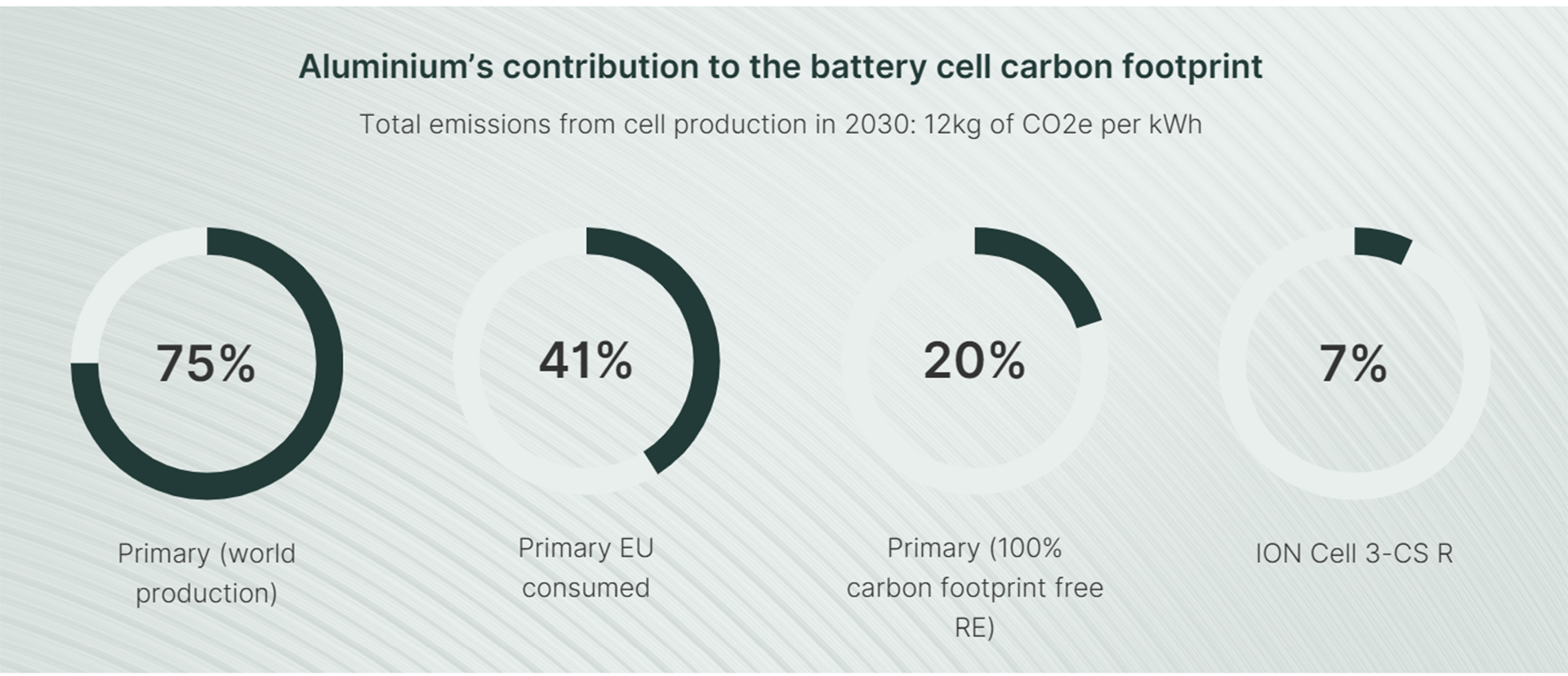
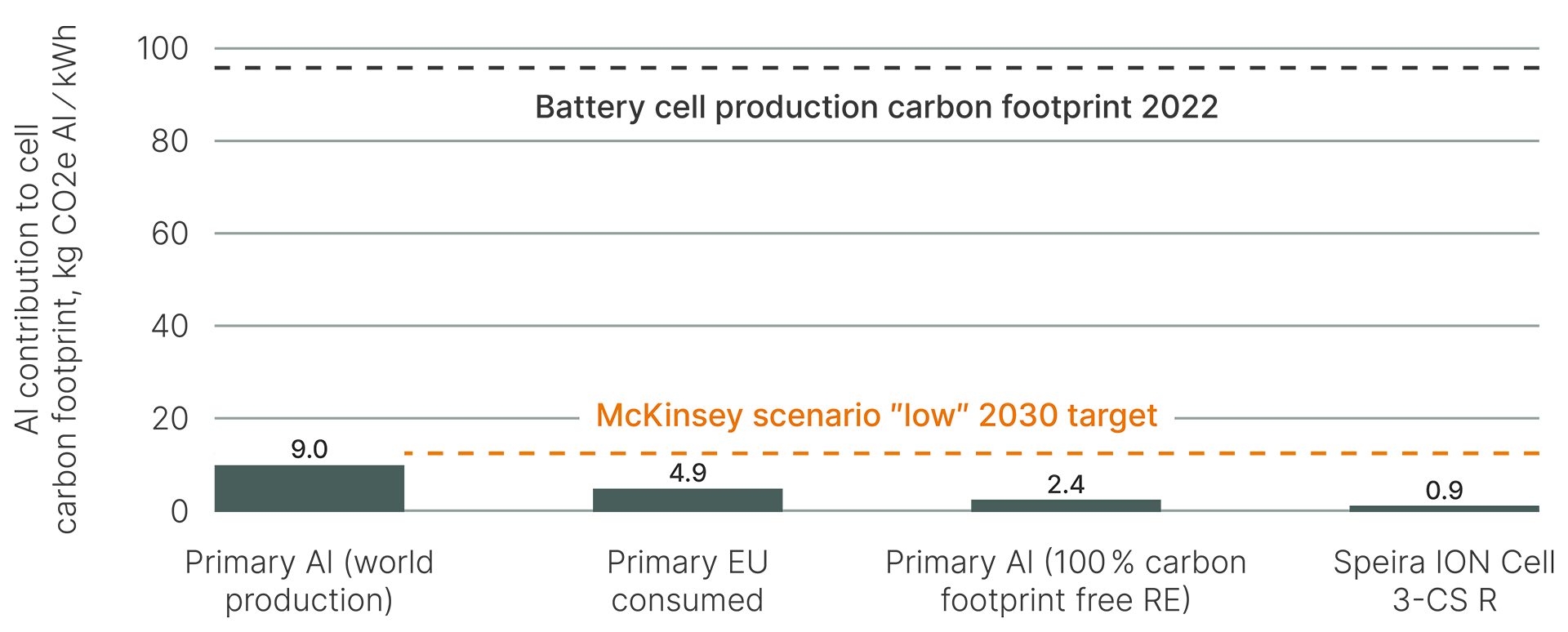
However, the use of primary aluminium produced with 100% carbon-footprint-free REs and the application of material featuring a very high recycled content, such as Speira ION Cell 3-CS R, provide a pathway to significant reductions in greenhouse gas emissions. The use of Speira ION Cell 3-CS R would reduce the share of emissions from aluminium components in the total greenhouse gas emissions from lithium-ion battery cell production to about 7%.
However, this high-level assessment neglects the complexity of component requirements and material properties required for reliable, safe, and efficient batteries. Therefore, a more detailed evaluation has been performed that separately considers aluminium foil used as a cathode current collector (also known as an electrode foil) and as cell housings.
Want to know more about Speira ION for cell housing and cathode foil and its contribution to battery cell carbon footprint? Check out the details here.
Please note, this article will also appear in the 19th edition of our quarterly publication.