Professor Simon Litsyn, CEO of XtraLit Ltd, discusses the problems associated with traditional lithium extraction methods and explains how the company’s Direct Lithium Extraction technology can mitigate these challenges.
Lithium extraction from brines with low concentrations
Problem: In the revolutionary era of the green energy transition, a significant increase in the production of electric batteries is required. Modern battery technology is mainly based on the use of lithium. A substantial part of the lithium extraction is currently done by long-term evaporation of salt water with a high concentration (more than 1 g/l) of this element. Such water sources are limited and cannot meet the demand for the required amount of lithium. Without the introduction of new technologies, by 2030 the demand for lithium will be met by less than half. In addition, the existing technologies are extremely ecologically harmful.
Solution: XtraLit has developed revolutionary innovative technology for direct extraction of lithium from aqueous sources with medium and low concentrations (up to 500 mg/l). It is based on using a proprietary patented sorbent in ion exchange.
Compared to other technologies, the method has a significantly higher selectivity to lithium – an increase in the concentration of lithium in the brine by two-three orders of magnitude along with a similar drop in the concentrations of other elements, as well as increased capacity and durability of the sorbent.
Moreover, the technology provides a unique solution for lithium extraction from brines with very low concentrations (5-100 mg/l). The use of XtraLit technology allows for the significant expansion of the available resources for extraction, including salt lakes, technical brines accompanying the oil extraction, and geothermal waters.
The technology is protected by patents, has been tested and is in the stage of pilot testing. Production of up to a ton of sorbent per year has been established. Estimation of the cost of extracting a ton of lithium carbonate by our method (without capital investments) is less than $4,000 per ton of lithium carbonate.
Abundance of lithium
There is plenty of lithium in nature. The world’s oceans contain an estimated 180 billion tons of lithium. But it is diluted, present at roughly 0.2 parts per million (ppm). Unfortunately, there is currently no technology for economically justified lithium extraction from such low concentrated sources. However, development of technologies allowing for the production of lithium from relatively low concentrations could expand our ability to cover the industrial needs in this chemical element.
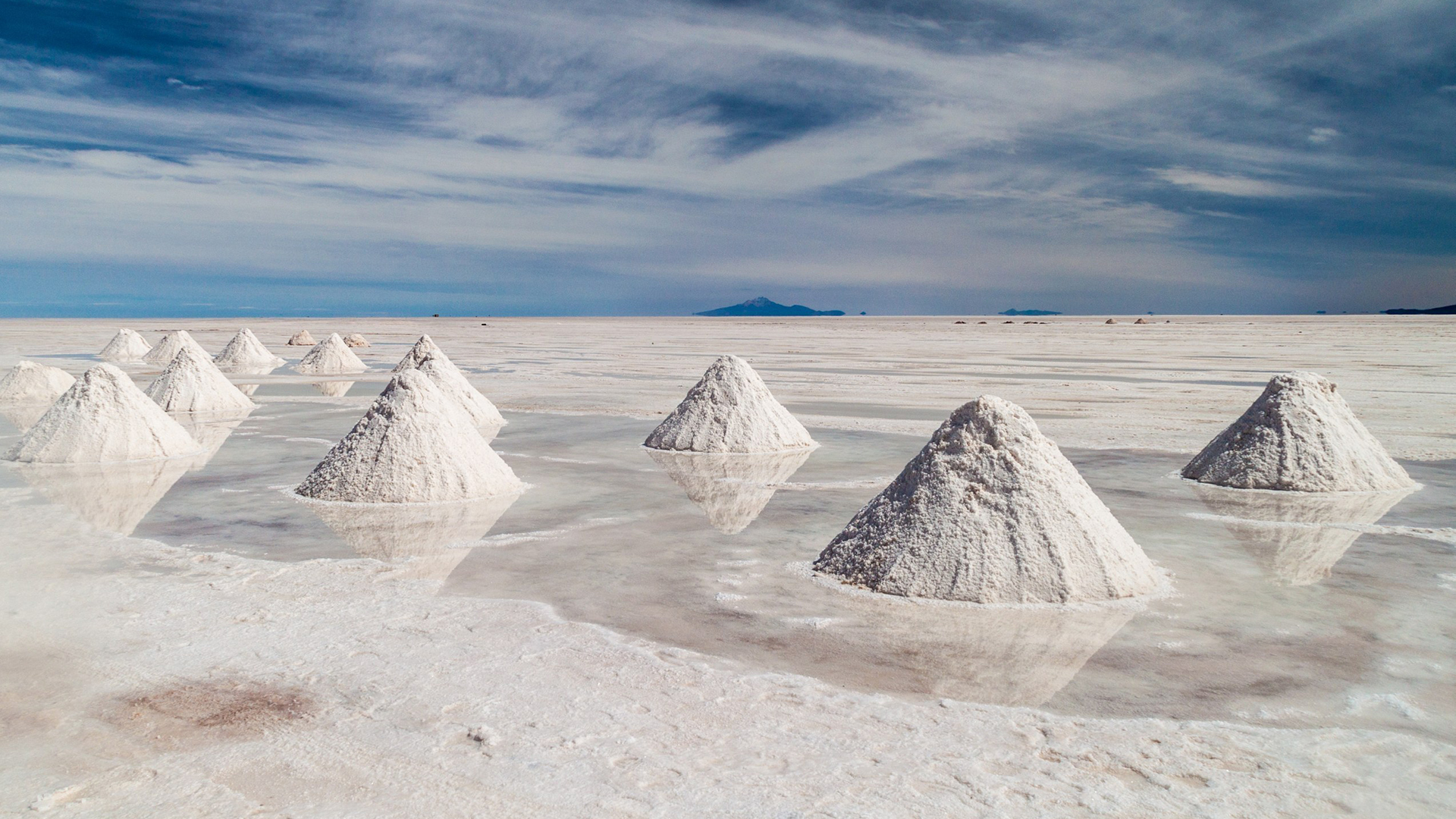
Direct Lithium Extraction processes
The traditionally used processes for lithium extraction are based either on hard-rock mining (mainly in Australia) or natural brine evaporation (mainly in South America). Direct Lithium Extraction (DLE) uses an alternative process that involves a highly selective absorbent to extract lithium from brine water. The solution extracted from the brine water is then polished of impurities to yield high-grade lithium carbonate and lithium hydroxide.
Reasons for exploration and development of low-concentration lithium brines with DLE include:
- Environmental impact (CO2emissions, land footprint, freshwater use, waste management, chemicals use, and impact on local ecosystem) is much lower for DLE than for conventional methods. A number of major conventional lithium projects have been delayed or cancelled because of environmental issues or other environmental, social, and governance (ESG) considerations;
- Geopolitical risks of a high geographical concentration of conventional lithium projects
under operation or development. 75% of lithium reserves and 90% of production are in
three countries only (Chile, Australia, China). The high concentration of reserves and production to very few countries raise concerns for the security of future lithium supplies. Low concentration lithium brines are well known all over the world; - Committed lithium production (operating and under construction) which comes from the
conventional projects only, covers less than 40% of 2030 lithium demand. It takes less time to develop DLE projects than conventional projects (7-10 years for conventional projects, 2-5 years for DLE projects); and - Lower or comparable capital expenditure (CapEx) and operational expenditure (OpEx) for DLE in comparison with conventional projects.
Low-concentration lithium brines potential sources
Lithium brines with concentrations of less than 300 mg/l usually cannot be developed by conventional evaporation methods. Lithium resources in brines with lithium concentrations of less than the cut-off grade for conventional lithium brines are by the order of magnitude greater than conventional resources.
Until recently, lithium brines with concentrations less than 300 mg/l or lithium brines with larger concentrations in non-arid regions where natural evaporation is not feasible have never been an exploration target for lithium. Most of these lithium brines were discovered accidentally in oil and gas produced water, in geothermal fluids for power stations, and while exploring for high-concentration lithium brines in salars (salt flats). Nevertheless, tens of millions of tons of lithium in low-concentration brines have been discovered already. So, there is no doubt that dedicated exploration for low-concentration lithium brines will lead to the discovery of many additional large, economically viable lithium deposits.
High-concentration lithium brines are accumulated mainly in salars, while lower lithium concentrations of 10-300 mg/l can be found in salt lakes, geothermal brines, deep underground, and in oilfield brines.
Salt lakes with lithium concentrations of 30-100 ppm are known in Israel and Jordan (Dead Sea), Turkmenistan (Kara-Bogaz-Gol), the US (Great Salt Lake), and China. The key processes accountable for the lithium enrichment in oilfield brines are the dissolution of lithium-enriched evaporites or fluid-rock interaction with lithium-bearing minerals in sedimentary, magmatic, or metamorphic rocks. These brines with lithium concentrations of 10-300 mg/l are known in the US, Canada, Russia, Kazakhstan, Uzbekistan, and other countries.
Lithium concentrations in produced water from US unconventional oil and gas fields vary between 5 and 150 mg/l. The most promising for Direct Lithium Extraction are the Smackover Formation in Arkansas, Marcellus Shale in the north-eastern part of US, the Bakken Formation of the Williston Basin in North Dakota, Montana (US) and Saskatchewan (Canada), and the Permian Basin in Texas.
Lithium in geothermal brines comes from magmatic or volcanic activity and hot water-rock interaction. Geothermal waters with lithium concentrations of up to 300 mg/l are known all over the world. Salton Sea is the most prospective site for lithium extraction in the US. Significant geothermal lithium resources have been identified in Europe in Italy, France, UK, Germany, and Turkey. Geothermal lithium brines are known also in New Zealand, Ireland, Indonesia, and other countries. DLE technology is the only way to develop these deposits.
Types of DLE technologies
There are three main types of DLE technologies: ion exchange, sorption, and solvent extraction. DLE technologies all interact with lithium ions exclusively and leave all the other ions in the solution unchanged.
Sorption technology
Lithium chloride (LiCl) molecules physically ‘stick’ onto the surface of a sorbent – normally a resin-like substance. The resin then becomes a lithium-loaded solution and is later ‘washed’ with a stripping solution that retains the LiCl. This regenerates the sorbent to be used in further adsorption cycles.
Solvent extraction technology
A solvent, normally an organic liquid, exchanges LiCl molecules or lithium ions by forming complexes between itself and the lithium in brine.
Ion exchange (IX) technology
The sorbent – normally a solid – takes lithium ions from the solution by trading them for protons or other cations within the sorbent’s structure. Then, it is regenerated with an acidic solution that strips the sorbent and replenishes the cations.
An analysis shows that IX is the preferrable approach to address low concentrated sources.
XtraLit DLE
Sorbent characteristics are a critical factor in providing main advantages in the performance of the IX DLE method among various technology providers. XtraLit developed an IX DLE based on proprietary patented sorbent synthesised from an optimised mixture of metal oxides.
In comparison with alternative IX technologies, it has better capacity (ability to absorb lithium per unit of sorbent mass), lithium selectivity (change in the lithium concentration compared to changes of concentrations of competing ions), durability (number of cycles the sorbent can survive), cost, kinetics, and processing time. XtraLit DLE is an exclusive approach allowing processing brines with concentrations as low as 5-100 mg/l.
XtraLit as a company
The company was established in July 2021. As many as 15 brines with concentrations of 5-300 mg/l from different locations have been successfully tested in the company laboratories.
Agreements on joint exploitation of brine sources have been signed and/or work programmes have been agreed with companies from Israel, Jordan, Canada, the US, France, Turkey, and Argentina. Several demo pilots are in the process of installation at the partners’ premises. The current full production potential is about 70 thousand tons of lithium carbonate per year. The agreements include a plan for the joint creation of pilot production facilities and the preparation of the construction of full-scale production.
The sorbent is currently manufactured in a chemical plant with production capacity of 150 kg/day, to grow to 1,000 kg/day by the end of 2023. The company plans to achieve more than $100m in annual revenues over seven years.
The team
The company is managed by an experienced team of industry and academy veterans with specialisations in chemistry, electronics, and business, with outstanding achievements in the creation of high-tech companies.
Funds
A total of $25m has been raised up to now. The proceeds will be used to further optimise the technology, create an upscaled production of the sorbent, and to support pilot projects in accordance with signed contracts.
Please note, this article will also appear in the fourteenth edition of our quarterly publication.